Sizing an Industrial Air Compressor to Fit Your Needs
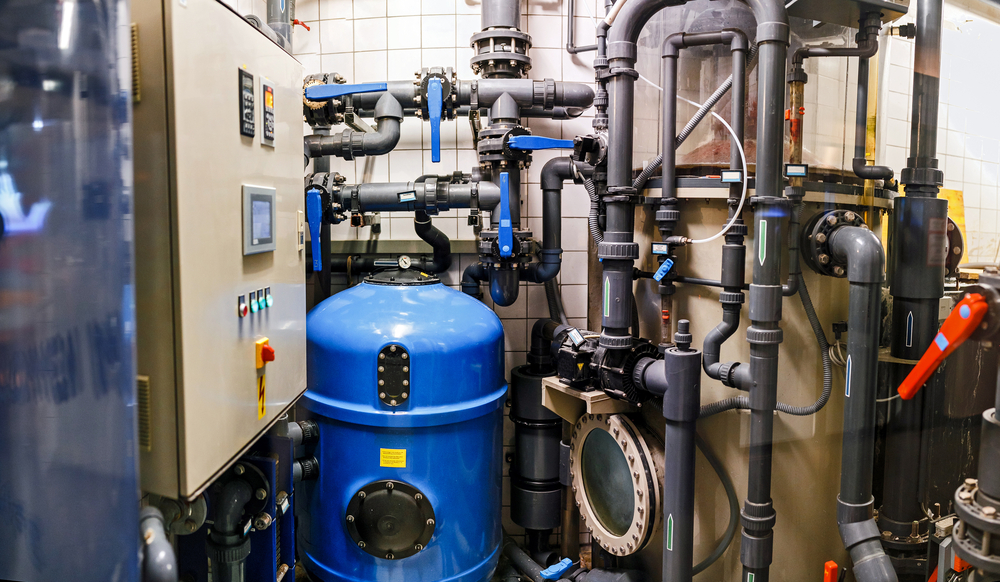
Sizing a new industrial air compressor can feel like a difficult task. It requires knowledge of the pressure and flow needed for the application. A solid understanding of how frequently jobs are performed and how many jobs are being completed at once. This may seem like a substantial amount of work, but the benefits of […]
Industries that Use Air Compressors Everyday
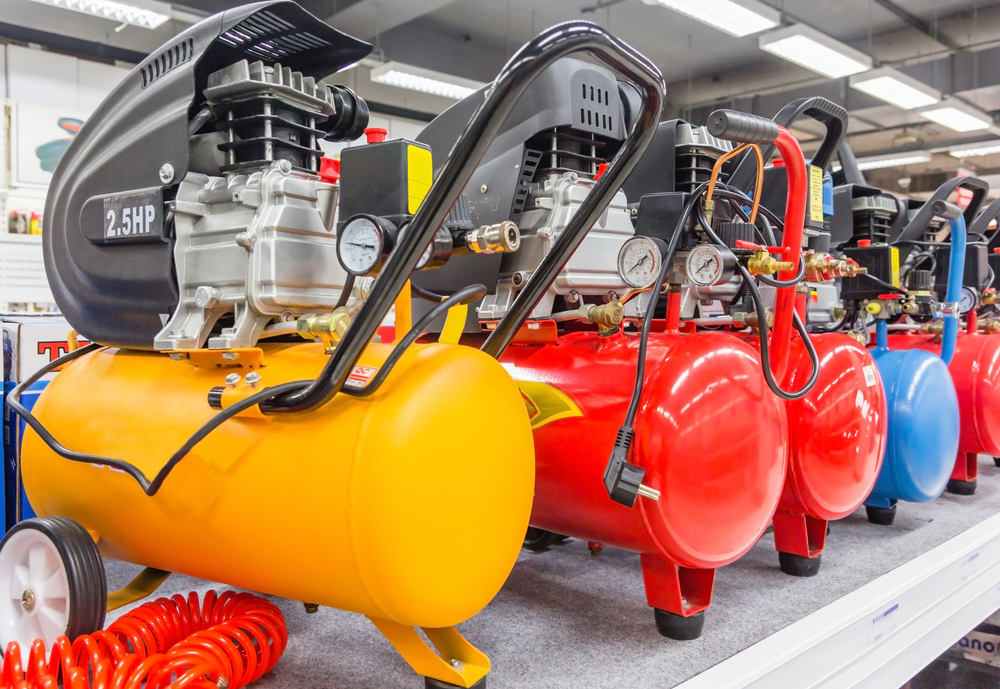
Dozens of industries have saved time and labor by using air compressors and have become reliant on them over the years. The applications of air compressors are nearly endless. For instance, the food you eat, the painkillers you take, the car you drive, and heck, even the chair you’re sitting on right now all have […]
Choosing the Right Air Compressor Oil: For Dummies
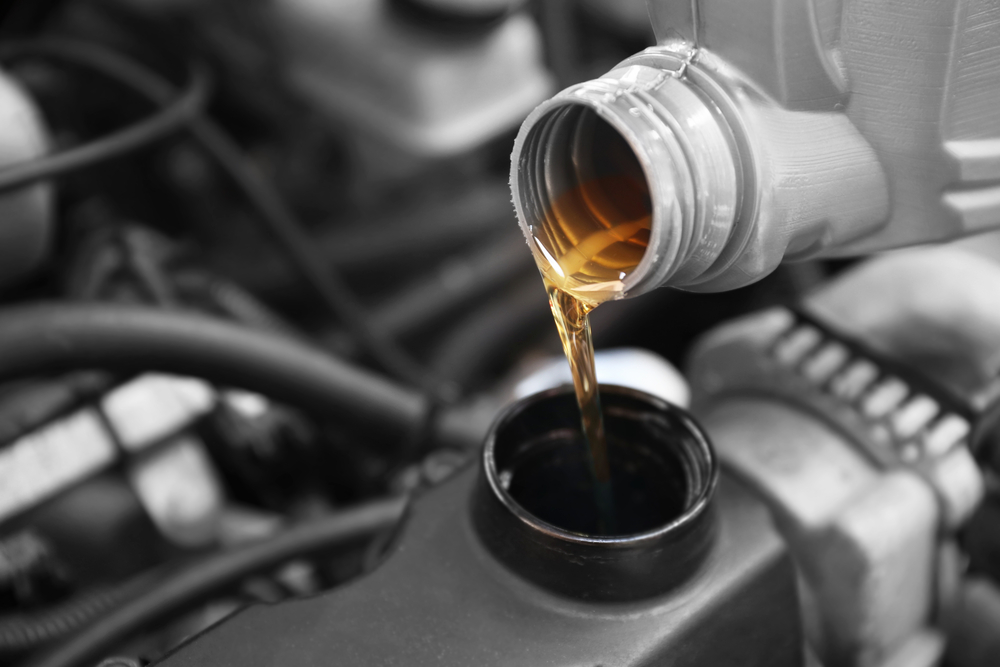
Just like different car models require a specific type and grade of oil for the best performance, the same is true for air compressors. When you use the right oil in your air compressor, it will benefit your machine in more ways than one. These benefits include a reduction in energy consumption, a decrease in […]
How to have a Healthy Relationship with Your Air Compressor
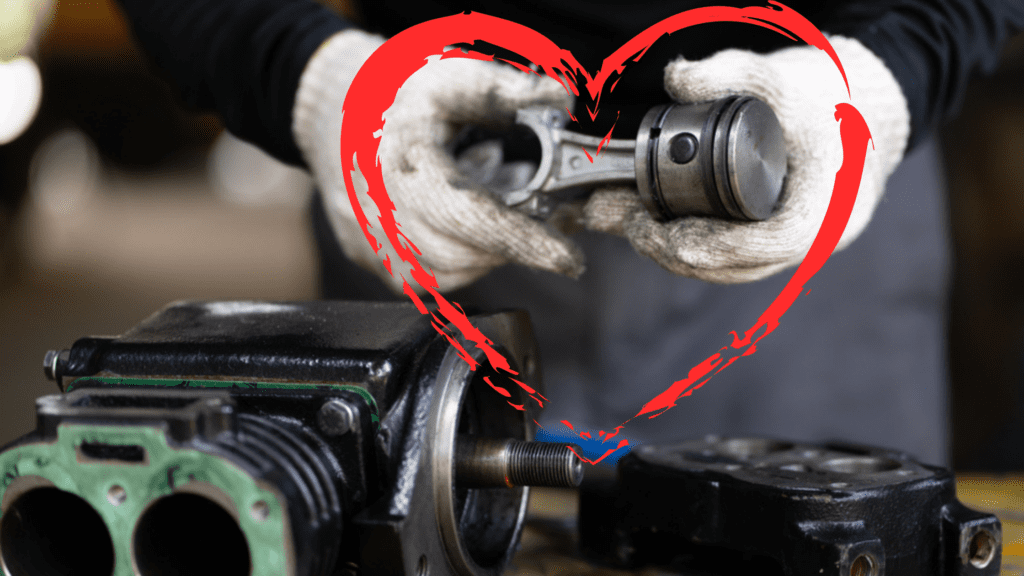
Unless you’ve been living in a cave your whole life, you know that today is Valentine’s Day. You may be celebrating with a significant other, treating yourself to a tub of ice cream, or hanging with some friends. But, have you ever thought about showing your air compressor system some love? With any healthy relationship, […]
Avoid Choosing the Wrong Industrial Compressor this Year!
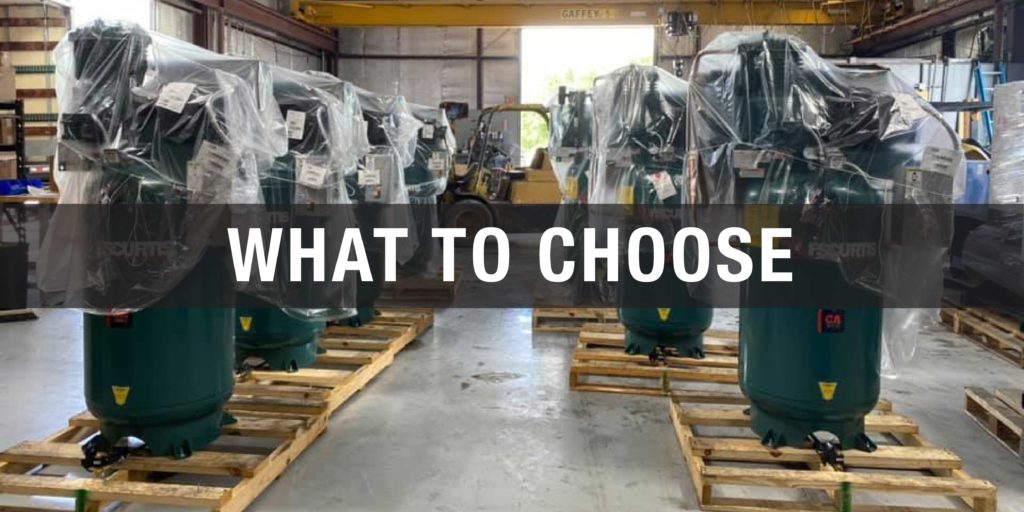
Choosing the right industrial compressor for your business can be tough. You have to sort through the compressors technologies, sizes, CFM (cubic feet per minute) and PSI (pounds per square inch) requirements, and other specs to determine which air compressor would best fit. Here are some common mistakes to avoid when choosing your industrial compressor: […]
Prepping your Air Compressor for Winter
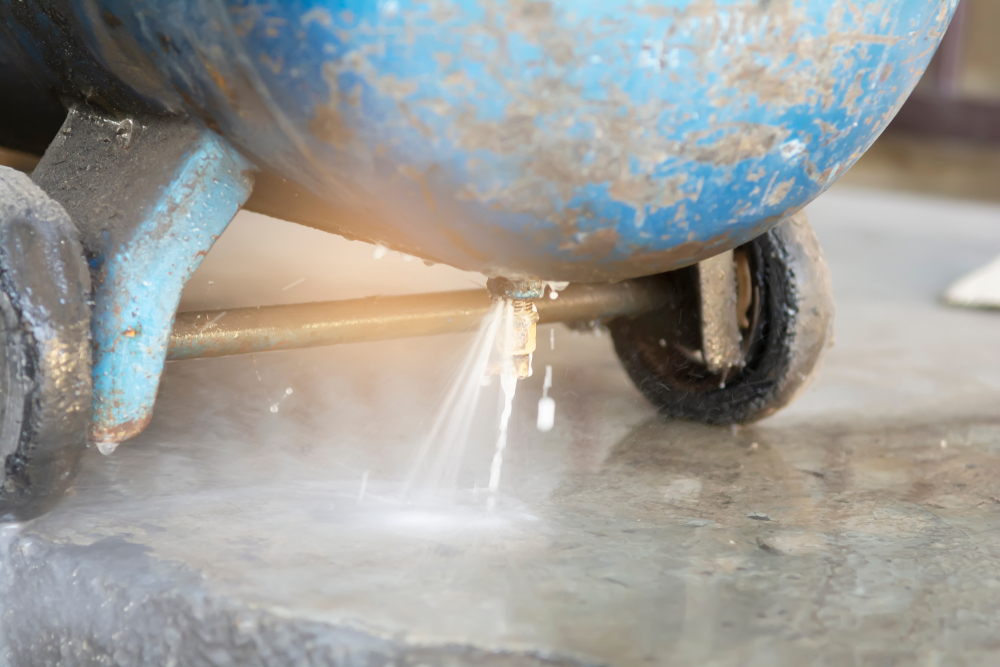
It’s getting to that time of the season where us Texans bring out our winter coats and slip on gloves before we head out to work. Just as we prepare ourselves for the winter months, our air compressors need some prep work to navigate properly through the cooler temperatures. Prepping your air compressor helps malfunctions […]
3C Loves Our Veterans
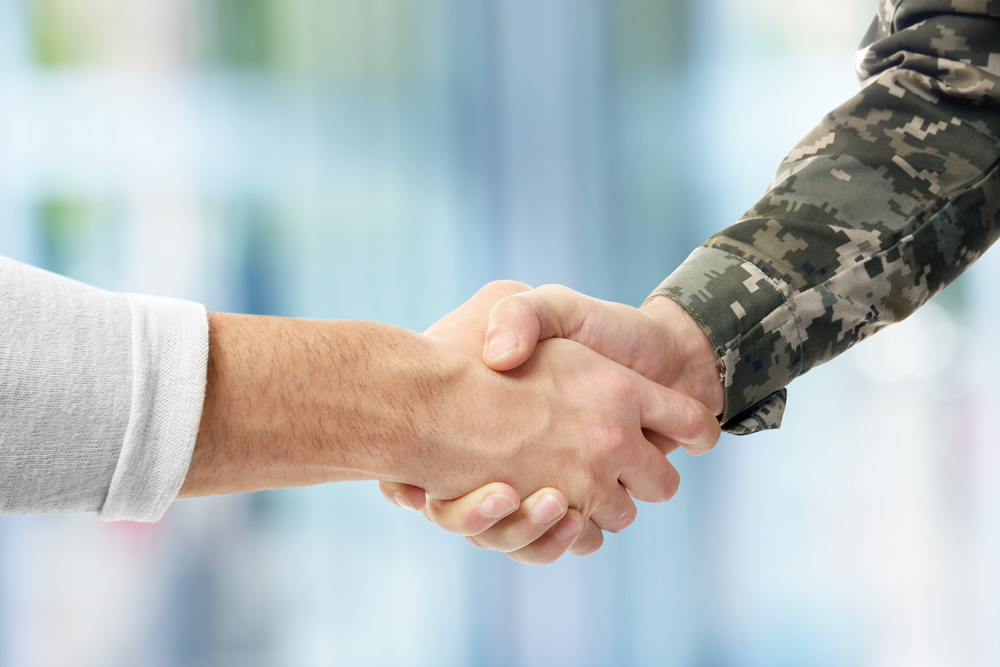
3C is proud to be a Veteran owned and operated company. We are honored to be a place of employment for other retired military men and women alike. In honor of Veterans Day, we are featuring a few of our Veterans on the 3C team. Meet Chase Stokley From 2013 – 2017, Chase served in […]
Do I Need a Desiccant or Refrigerated Air Dryer?
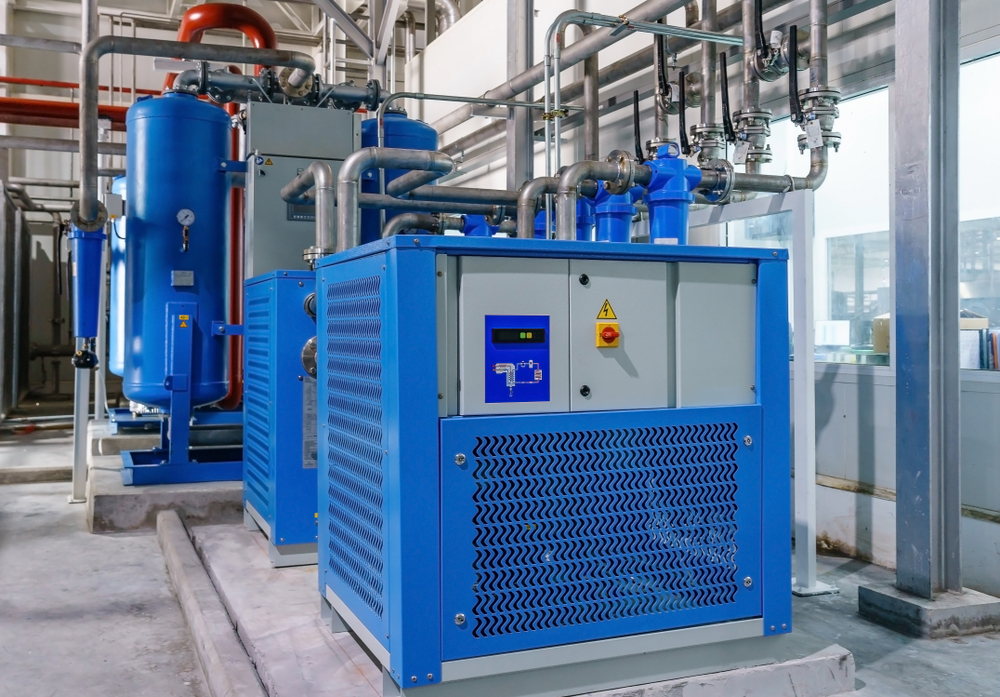
Air dryers are essential for the majority of compressed air applications. By nature, air compressors produce a lot of water. The atmosphere of air is compressed and the air gets very hot. When the air temperature decreases, the moisture that was in those atmospheres turns from a gas to a liquid. While some of the […]
Why Compressors Need Preventative Maintenance
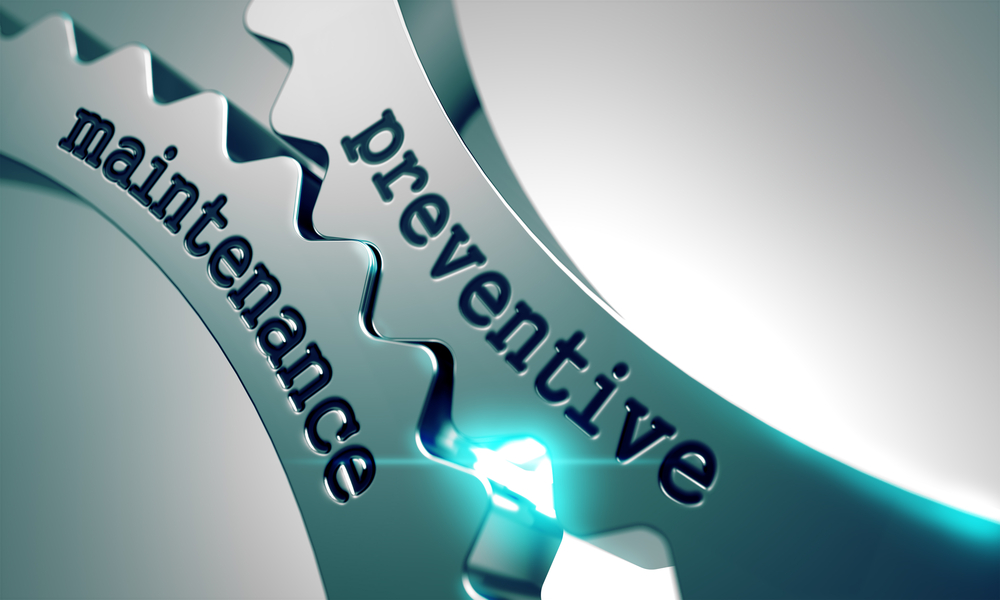
Air compressors are the backbone of the industrial world. They help make facilities all across the globe run smoothly and efficiently. However, air compressors are machines, and we must treat them that way. Instead of waiting around for a problem to arise, we must stay on top of our equipment. We call this preventative maintenance […]
Everything You Need to Know About Compressed Air Piping
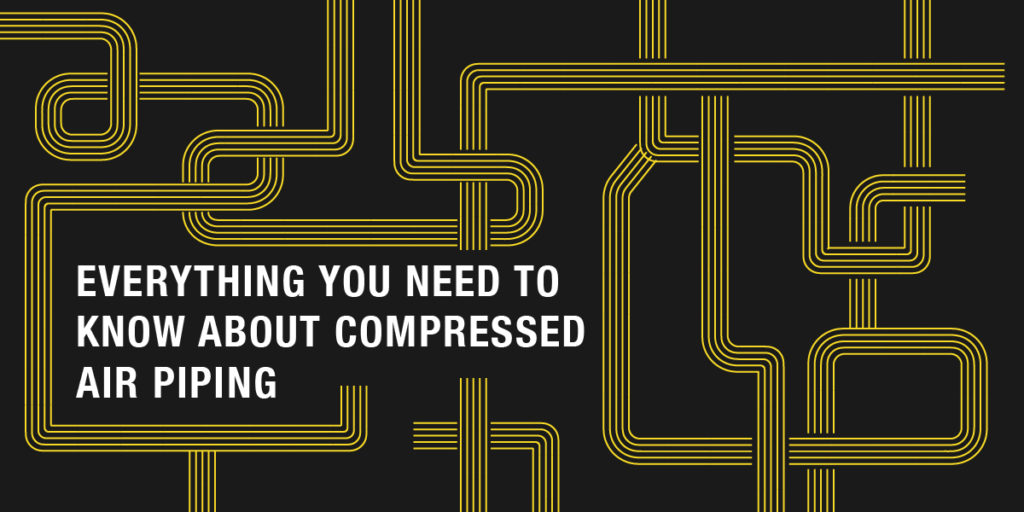
Traditional air piping is not always the most effective or efficient way to maintain your business. On top of that, you’ll also find your energy prices could be increasing. This where compressed air piping comes in. What is Compressed Air Piping? The purpose of an air piping system is to deliver compressed air to where […]