Choosing the Right Air Compressor Oil: For Dummies
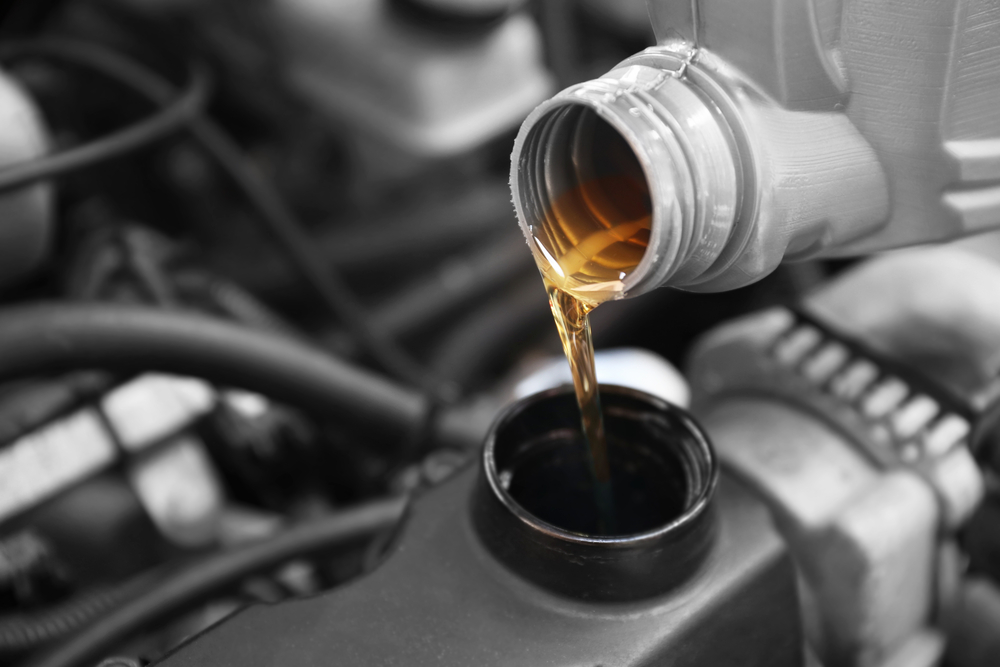
Just like different car models require a specific type and grade of oil for the best performance, the same is true for air compressors. When you use the right oil in your air compressor, it will benefit your machine in more ways than one. These benefits include a reduction in energy consumption, a decrease in […]
How to have a Healthy Relationship with Your Air Compressor
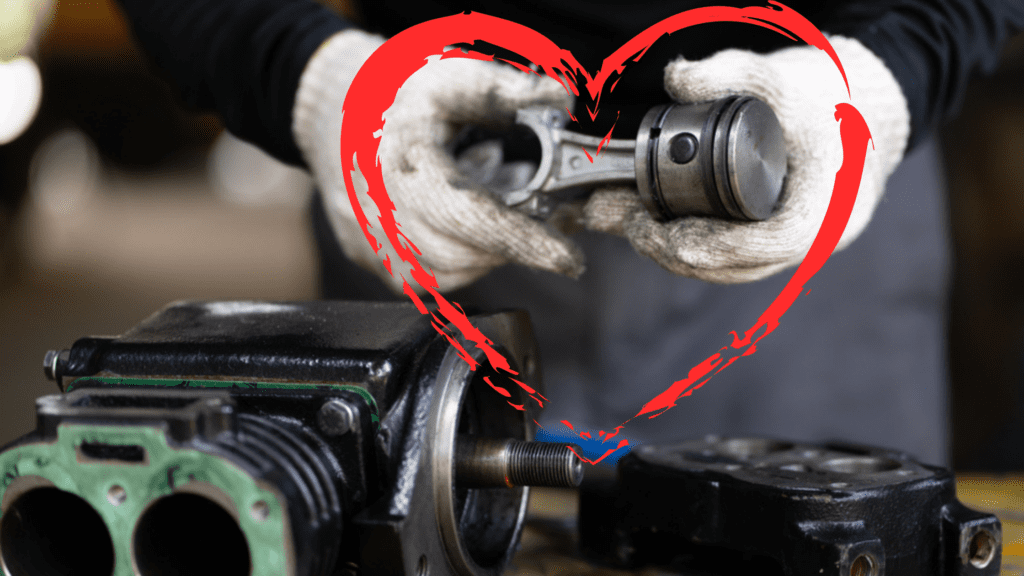
Unless you’ve been living in a cave your whole life, you know that today is Valentine’s Day. You may be celebrating with a significant other, treating yourself to a tub of ice cream, or hanging with some friends. But, have you ever thought about showing your air compressor system some love? With any healthy relationship, […]
Avoid Choosing the Wrong Industrial Compressor this Year!
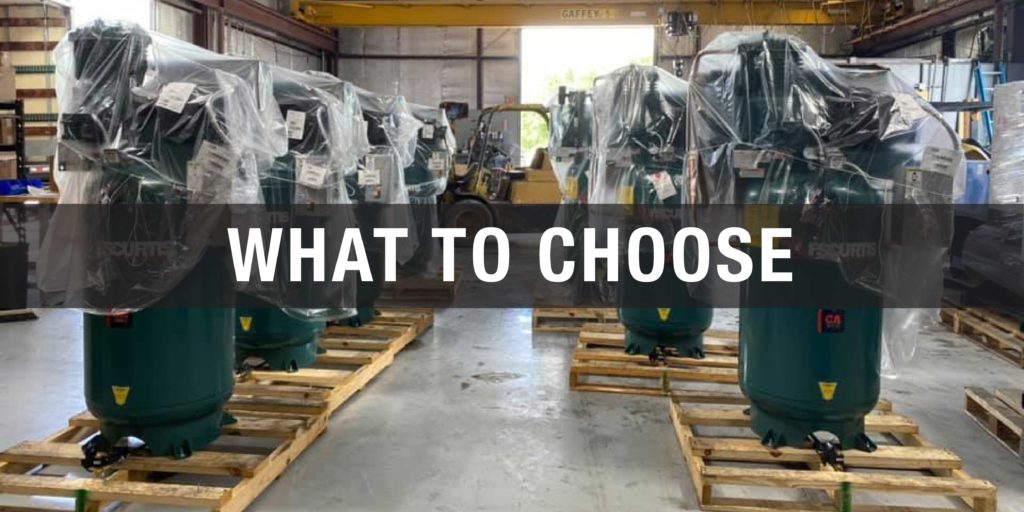
Choosing the right industrial compressor for your business can be tough. You have to sort through the compressors technologies, sizes, CFM (cubic feet per minute) and PSI (pounds per square inch) requirements, and other specs to determine which air compressor would best fit. Here are some common mistakes to avoid when choosing your industrial compressor: […]
Prepping your Air Compressor for Winter
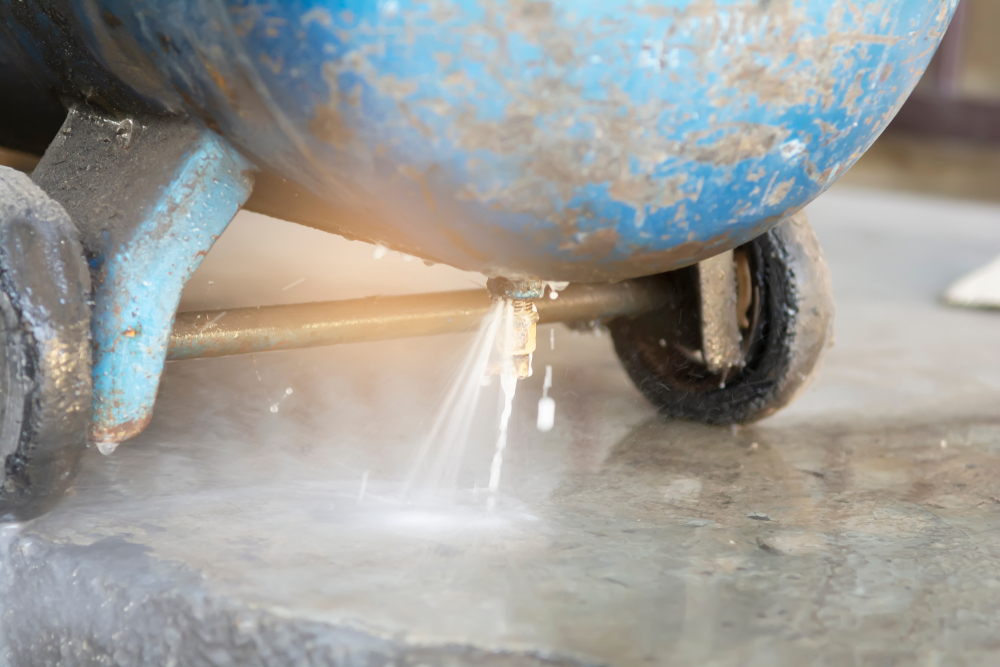
It’s getting to that time of the season where us Texans bring out our winter coats and slip on gloves before we head out to work. Just as we prepare ourselves for the winter months, our air compressors need some prep work to navigate properly through the cooler temperatures. Prepping your air compressor helps malfunctions […]
Why Compressors Need Preventative Maintenance
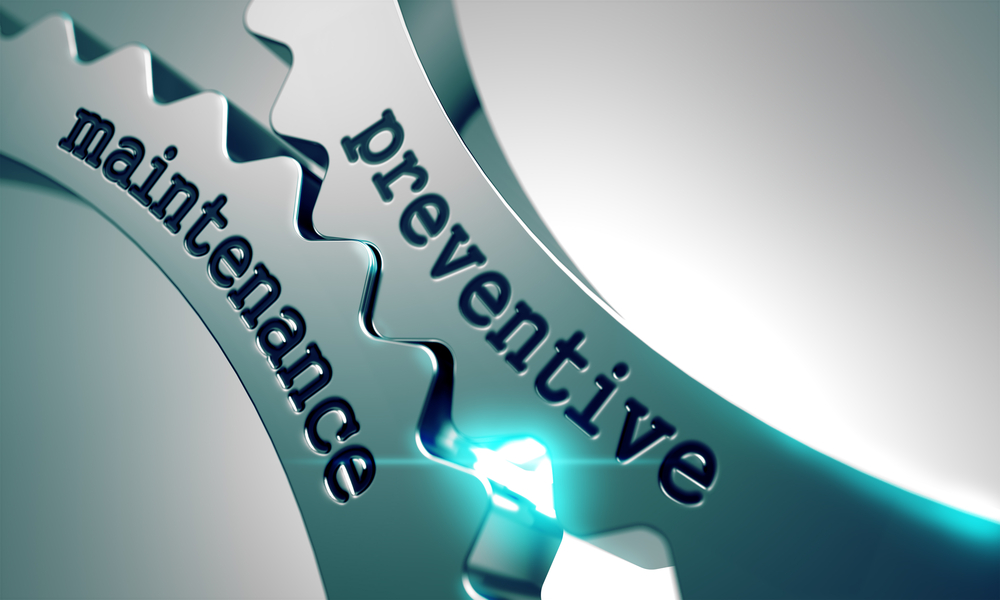
Air compressors are the backbone of the industrial world. They help make facilities all across the globe run smoothly and efficiently. However, air compressors are machines, and we must treat them that way. Instead of waiting around for a problem to arise, we must stay on top of our equipment. We call this preventative maintenance […]
Summer Maintenance Tips
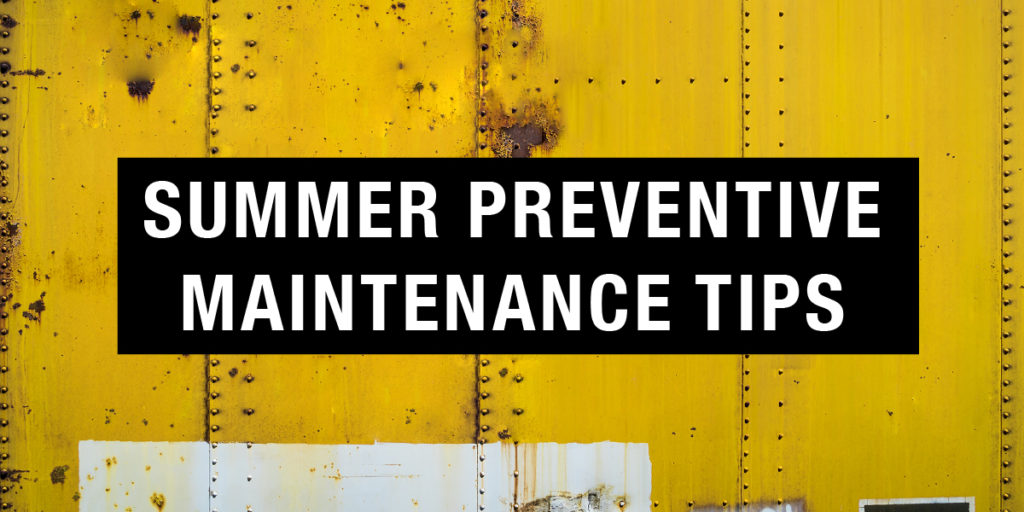
Summertime is officially here in Texas. The summer brings long, hot and humid days, all of which can take a toll on your air compressor. Skyrocketing temperatures combined with condensation can strain your equipment’s performance unless you’re prepared. Here are some summer maintenance tips that we at 3C have put together to help you with […]
Air Compressor Preventive Maintenance – What All Does it Entail?
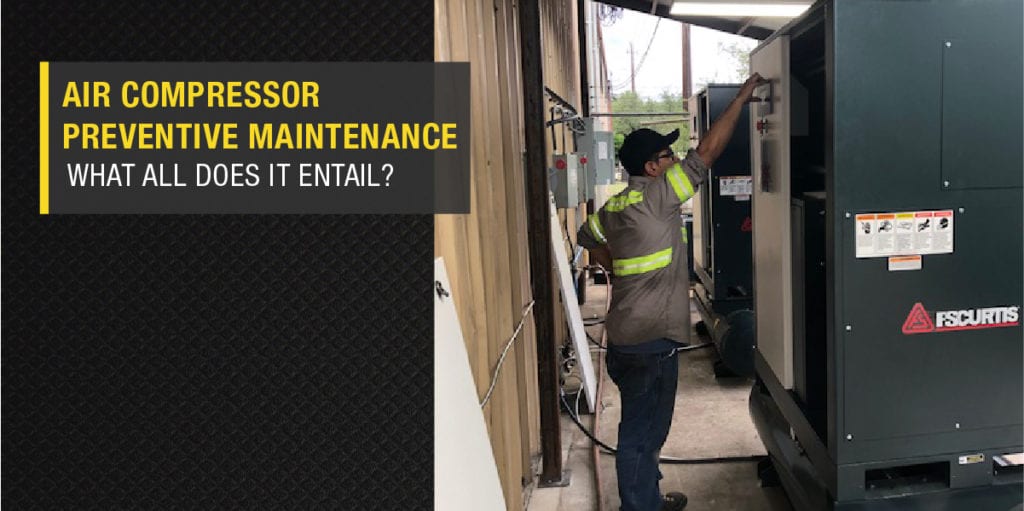
Preventive Maintenance is an essential part of keeping your air compressor running at optimal levels. Although PM can seem costly if you aren’t used to regularly servicing your compressor, the biggest expense you face is downtime should your equipment fail. What exactly is included in a PM service? There are two intervals at which you […]