How to have a Healthy Relationship with Your Air Compressor
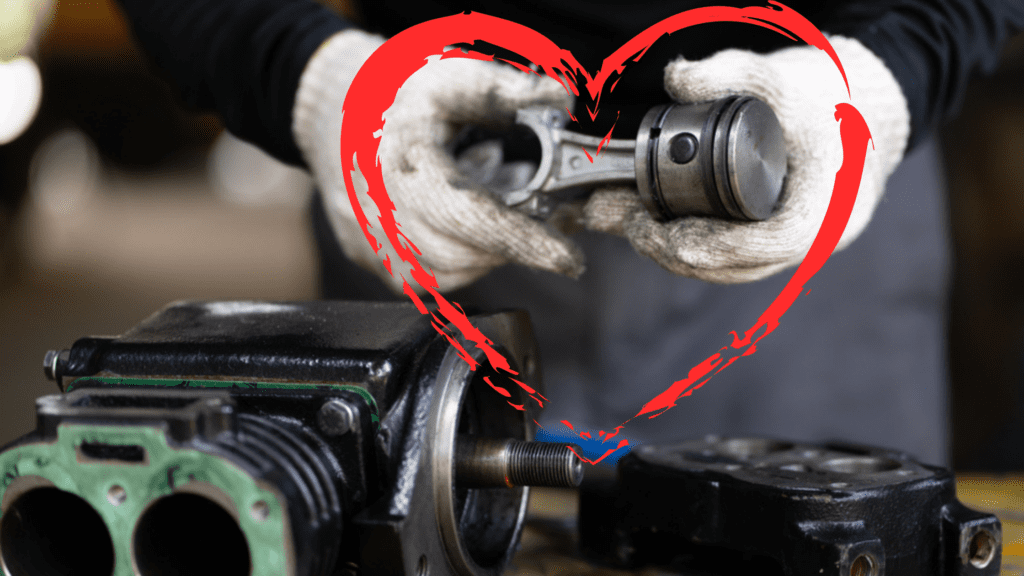
Unless you’ve been living in a cave your whole life, you know that today is Valentine’s Day. You may be celebrating with a significant other, treating yourself to a tub of ice cream, or hanging with some friends. But, have you ever thought about showing your air compressor system some love? With any healthy relationship, […]
Avoid Choosing the Wrong Industrial Compressor this Year!
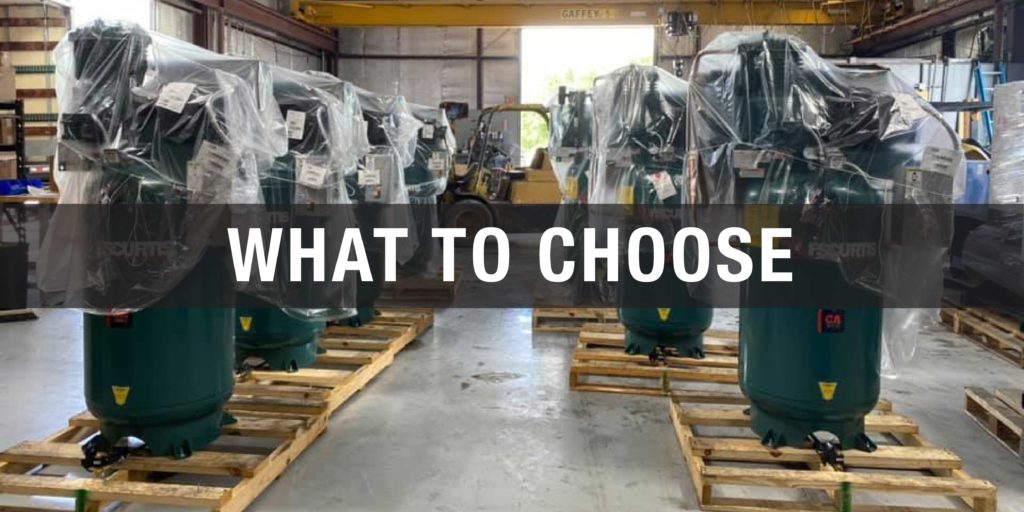
Choosing the right industrial compressor for your business can be tough. You have to sort through the compressors technologies, sizes, CFM (cubic feet per minute) and PSI (pounds per square inch) requirements, and other specs to determine which air compressor would best fit. Here are some common mistakes to avoid when choosing your industrial compressor: […]
Prepping your Air Compressor for Winter
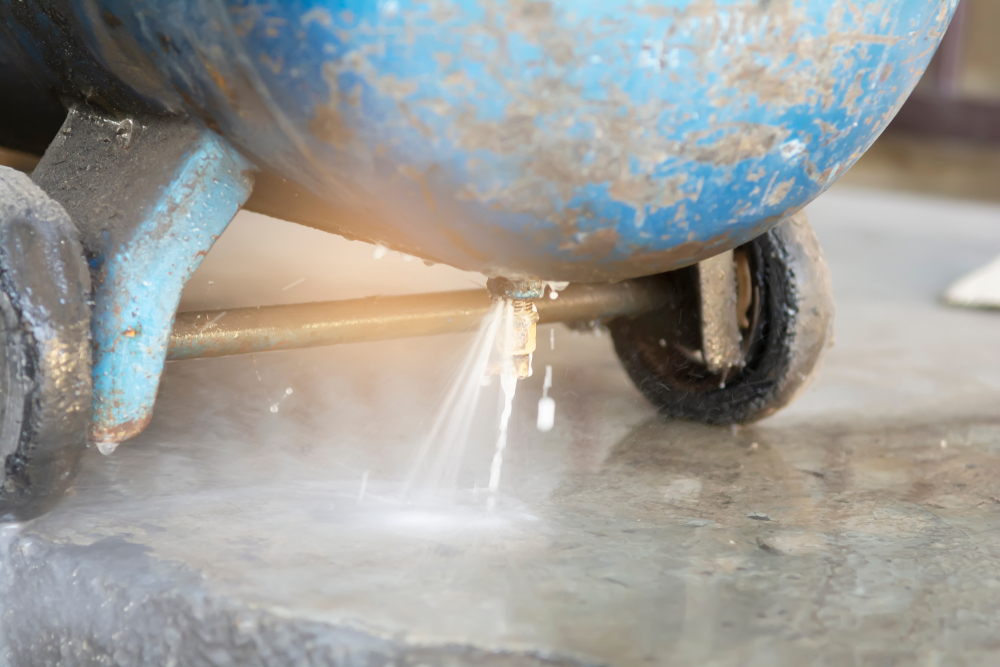
It’s getting to that time of the season where us Texans bring out our winter coats and slip on gloves before we head out to work. Just as we prepare ourselves for the winter months, our air compressors need some prep work to navigate properly through the cooler temperatures. Prepping your air compressor helps malfunctions […]
Which Air Compressor Is Right For You?
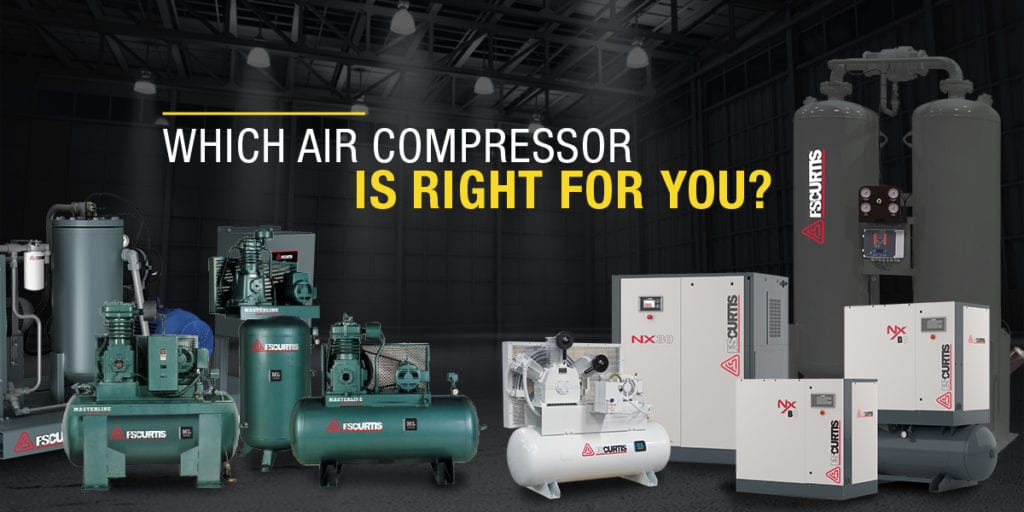
Choosing the Right Air Compressor Industries everywhere rely on air compressors to carry out a variety of functions, but not all compressors are the same. Here are some questions to ask yourself in order to determine which air compressor is right for you How much air do I need?Each tool or piece of equipment in […]
Air Treatment Mythbusting, Pt. 2
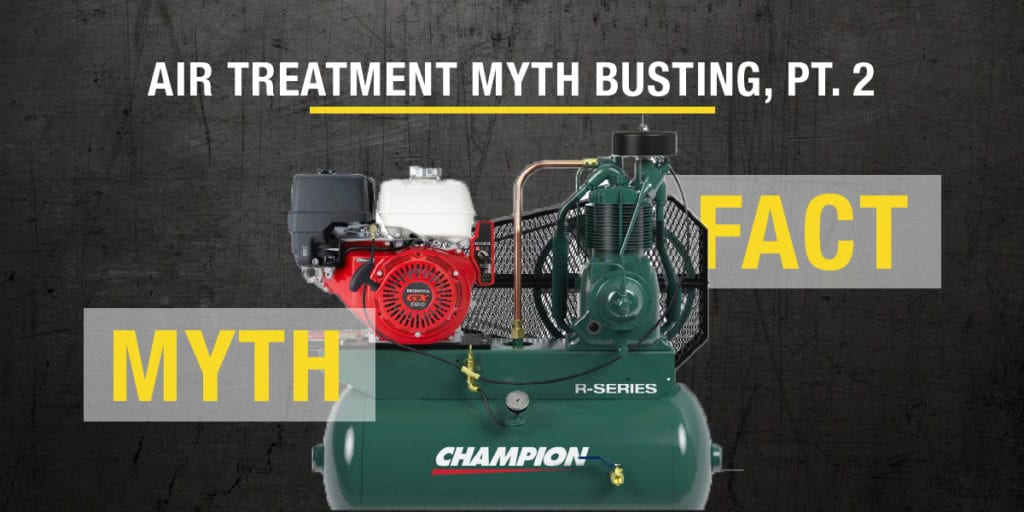
Myth: Compressed air contamination is a compressor issue. Fact: In a typical compressed air treatment system, contamination comes from three different sources, these being: Atmospheric air: Air compressors draw in huge amounts of atmospheric air, which continuously fills the system with contaminants such as water vapor, microorganisms, atmospheric dirt, and oil vapor. The air compressor: […]
Air Treatment Mythbusting, Pt. 1
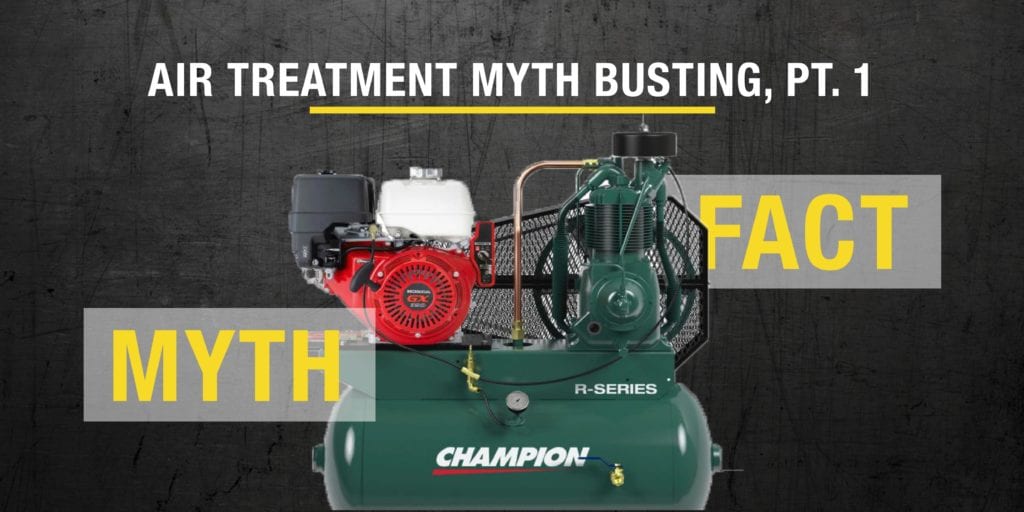
With the amount of information available on the internet about air treatment and compressors, it can be hard to decipher how much of it is actually true! This is where our expert mythbusting skills come into play! Here are some common myths and misconceptions about air treatment, debunked: Mythbusting: Filter elements should only be changed […]