How To Best Care for an Industrial Air Compressor This Summer
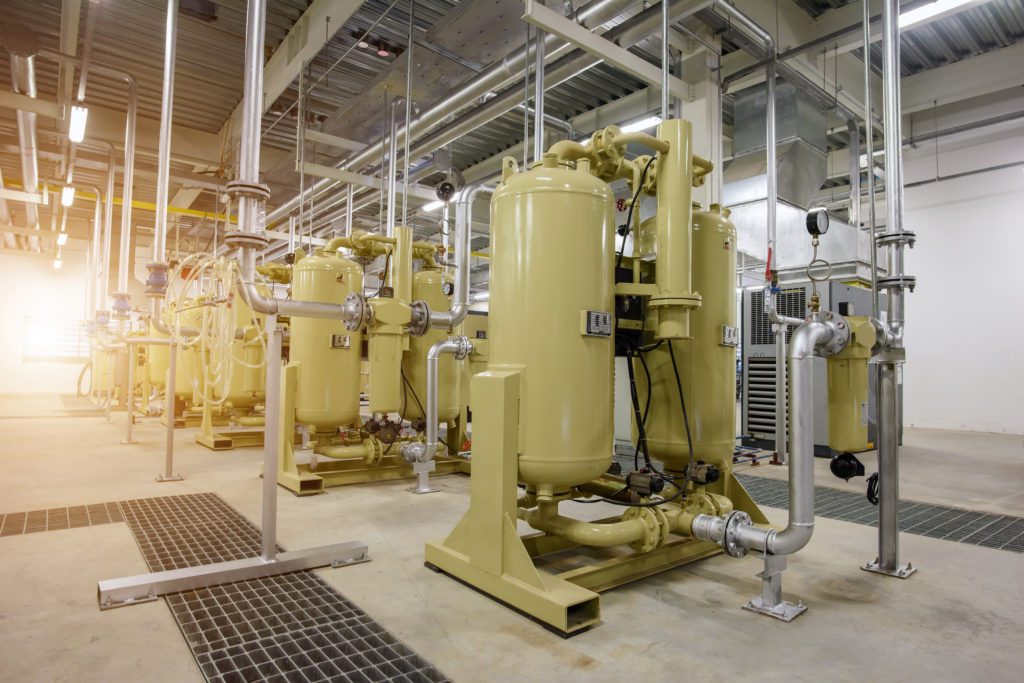
It may be a scorcher out there, but do not let your industrial air compressor unit suffer because of it this summer. Step 1: Choose The Right Industrial Air Compressor Choose the right air compressor and solidify your needs before selecting a unit: technology, size, ect. We suggest custom fabrication because curating your best option […]
Sizing an Industrial Air Compressor to Fit Your Needs
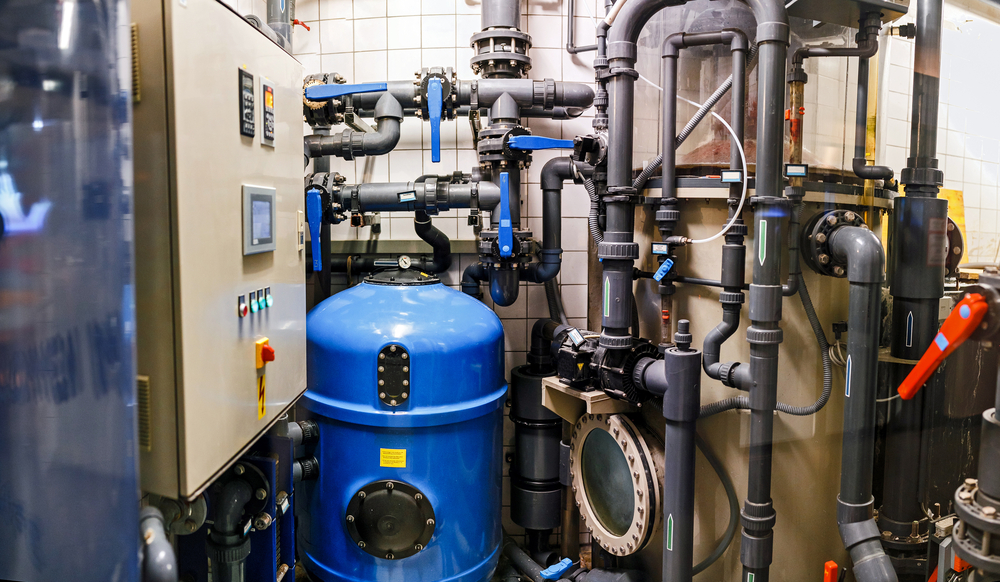
Sizing a new industrial air compressor can feel like a difficult task. It requires knowledge of the pressure and flow needed for the application. A solid understanding of how frequently jobs are performed and how many jobs are being completed at once. This may seem like a substantial amount of work, but the benefits of […]
Industries that Use Air Compressors Everyday
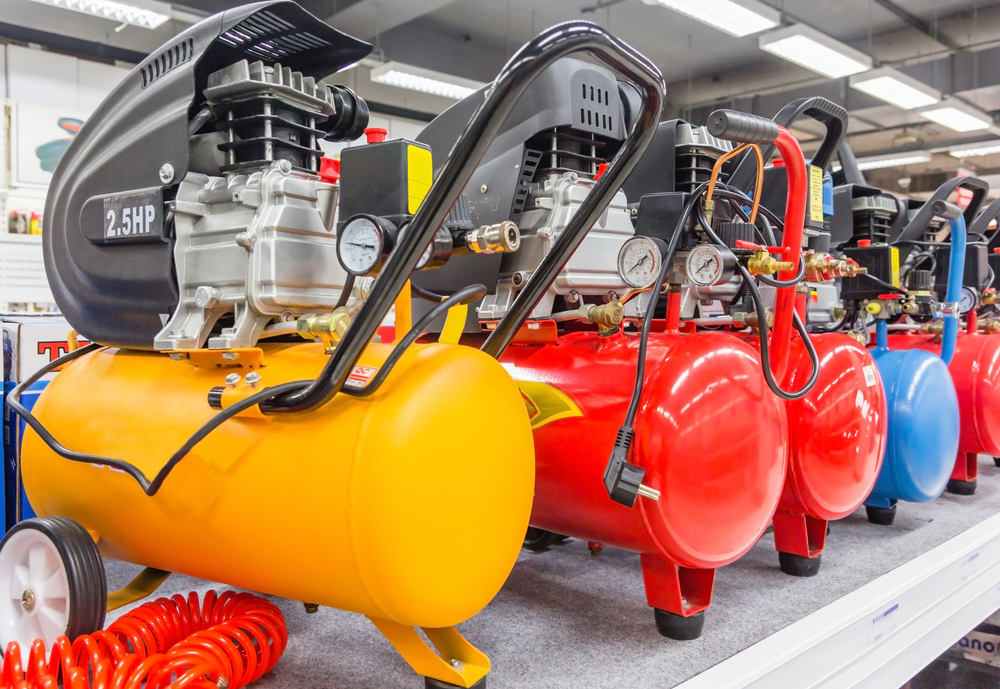
Dozens of industries have saved time and labor by using air compressors and have become reliant on them over the years. The applications of air compressors are nearly endless. For instance, the food you eat, the painkillers you take, the car you drive, and heck, even the chair you’re sitting on right now all have […]
Choosing the Right Air Compressor Oil: For Dummies
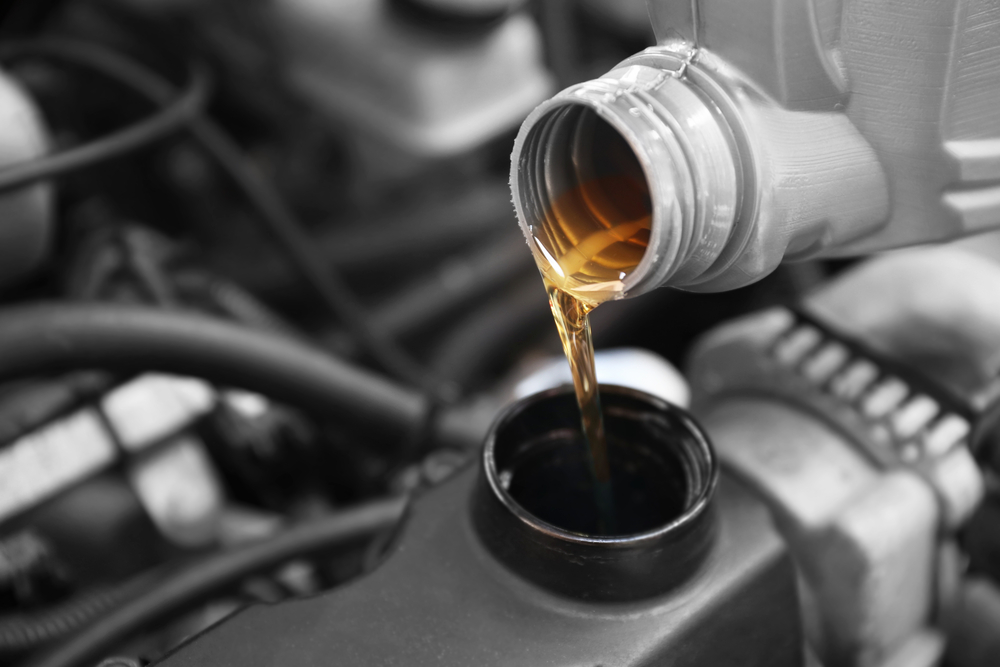
Just like different car models require a specific type and grade of oil for the best performance, the same is true for air compressors. When you use the right oil in your air compressor, it will benefit your machine in more ways than one. These benefits include a reduction in energy consumption, a decrease in […]
How to have a Healthy Relationship with Your Air Compressor
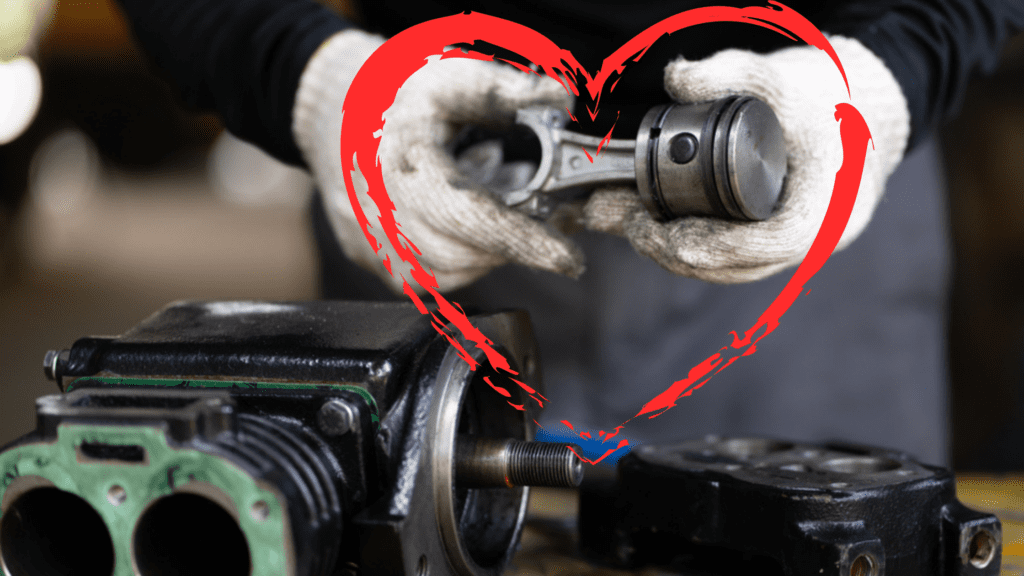
Unless you’ve been living in a cave your whole life, you know that today is Valentine’s Day. You may be celebrating with a significant other, treating yourself to a tub of ice cream, or hanging with some friends. But, have you ever thought about showing your air compressor system some love? With any healthy relationship, […]
Avoid Choosing the Wrong Industrial Compressor this Year!
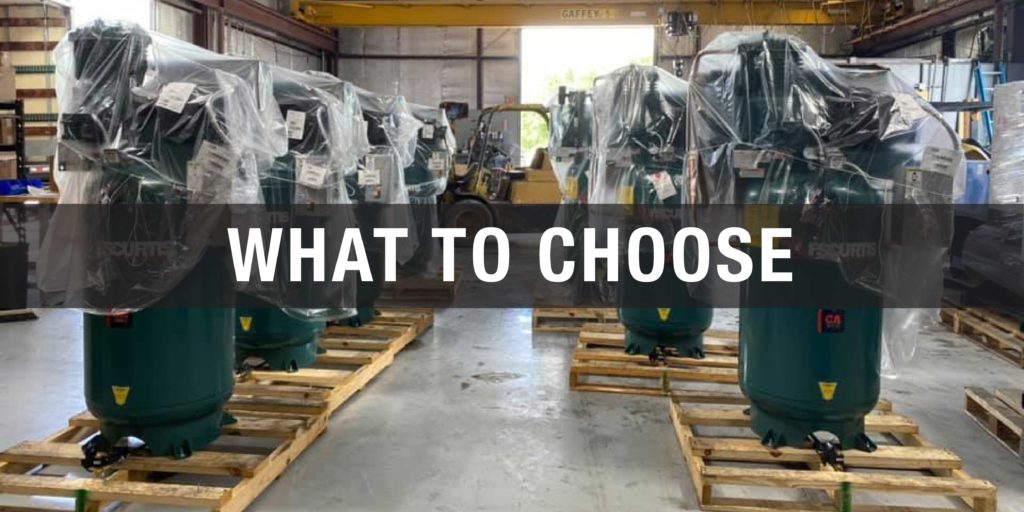
Choosing the right industrial compressor for your business can be tough. You have to sort through the compressors technologies, sizes, CFM (cubic feet per minute) and PSI (pounds per square inch) requirements, and other specs to determine which air compressor would best fit. Here are some common mistakes to avoid when choosing your industrial compressor: […]
Prepping your Air Compressor for Winter
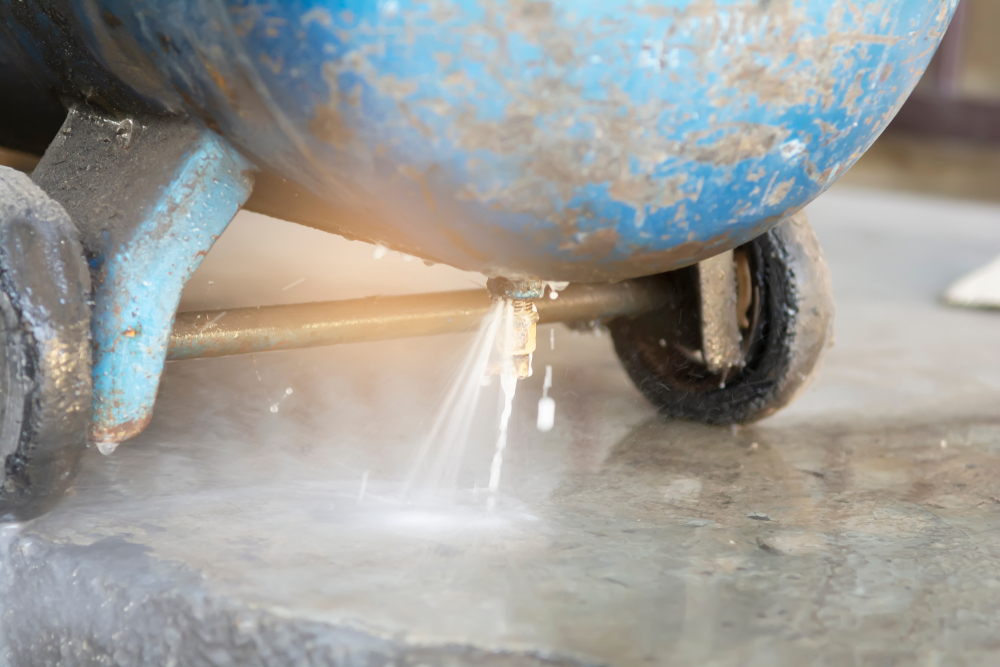
It’s getting to that time of the season where us Texans bring out our winter coats and slip on gloves before we head out to work. Just as we prepare ourselves for the winter months, our air compressors need some prep work to navigate properly through the cooler temperatures. Prepping your air compressor helps malfunctions […]
3C Loves Our Veterans
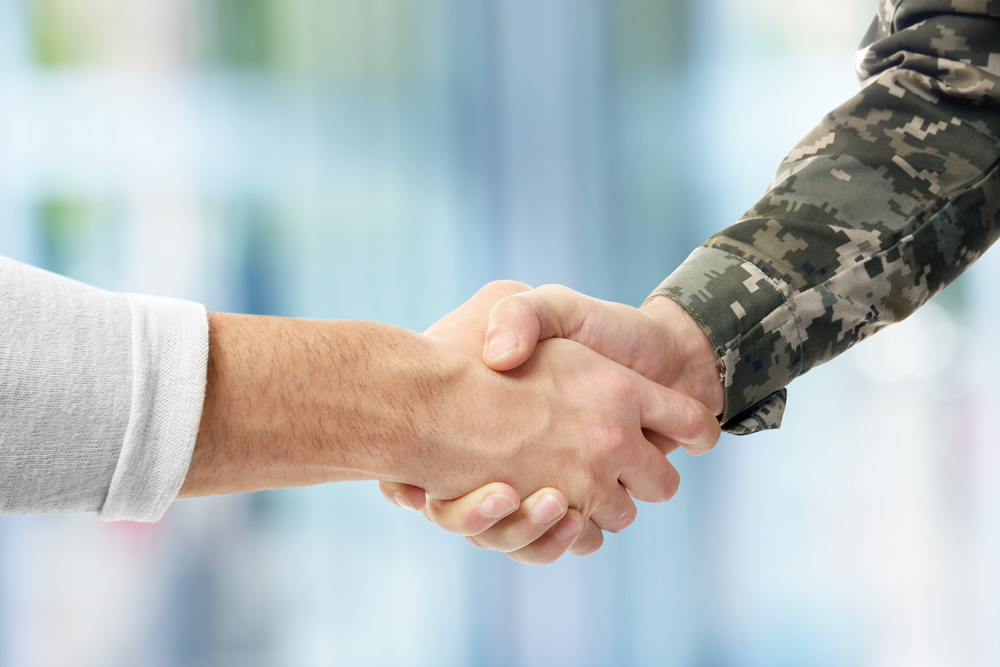
3C is proud to be a Veteran owned and operated company. We are honored to be a place of employment for other retired military men and women alike. In honor of Veterans Day, we are featuring a few of our Veterans on the 3C team. Meet Chase Stokley From 2013 – 2017, Chase served in […]
Why Compressors Need Preventative Maintenance
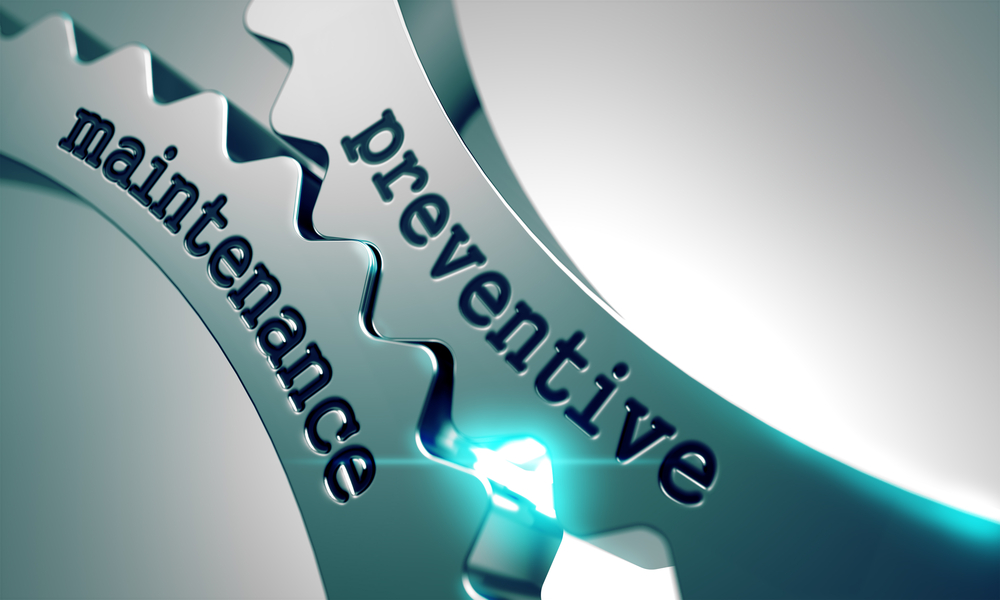
Air compressors are the backbone of the industrial world. They help make facilities all across the globe run smoothly and efficiently. However, air compressors are machines, and we must treat them that way. Instead of waiting around for a problem to arise, we must stay on top of our equipment. We call this preventative maintenance […]
Air Compressor Preventive Maintenance – What All Does it Entail?
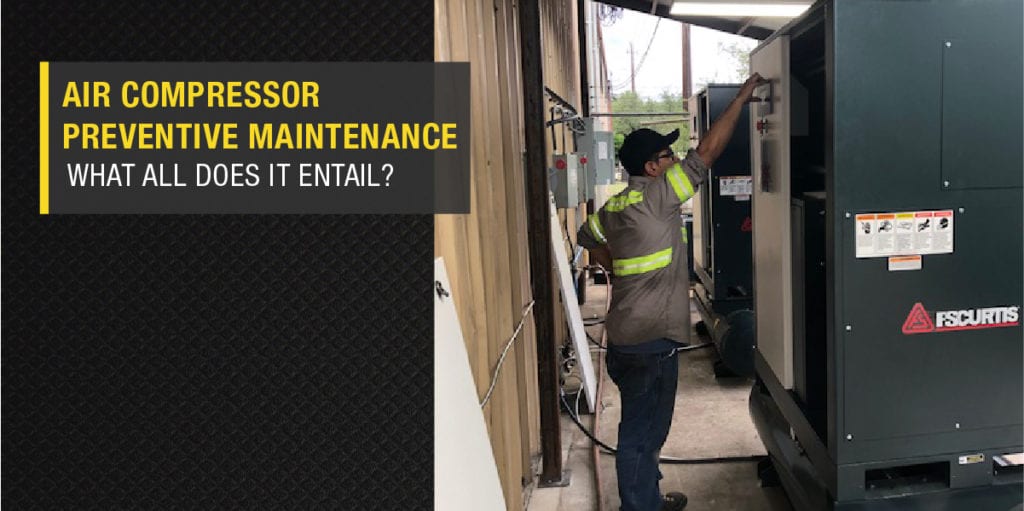
Preventive Maintenance is an essential part of keeping your air compressor running at optimal levels. Although PM can seem costly if you aren’t used to regularly servicing your compressor, the biggest expense you face is downtime should your equipment fail. What exactly is included in a PM service? There are two intervals at which you […]