Air Compressor Experts Separate Myths & Facts
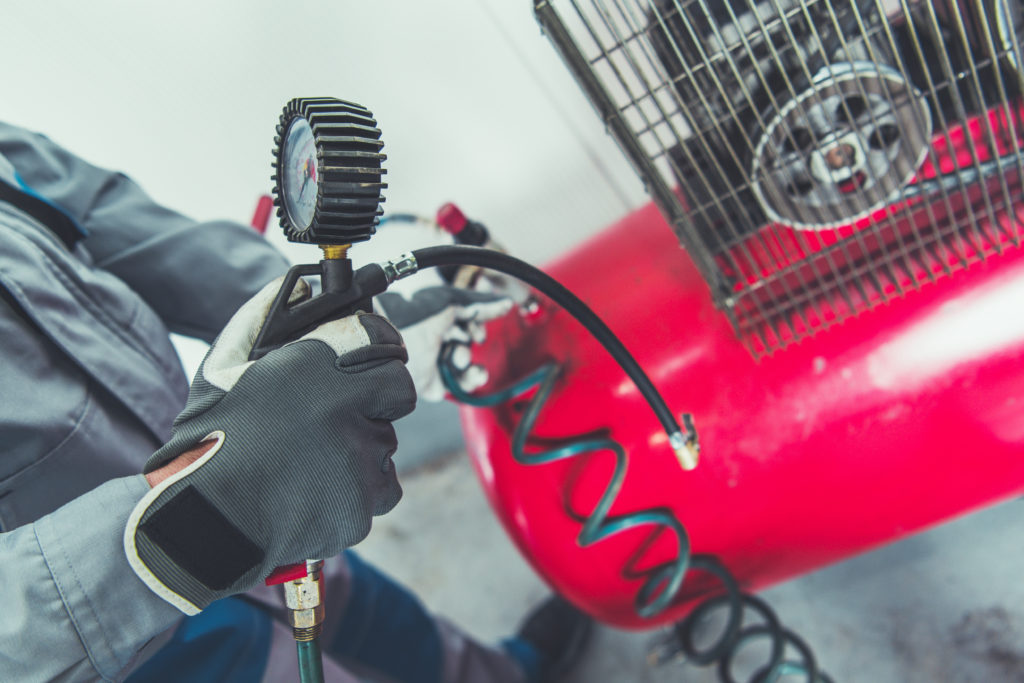
As your air compressor experts, 3C Industrial is committed to educating our clients about common misconceptions. How can you tell what is fact versus myth when it comes to air compressors?
Economic Advantages of the Industrial Air Compressor
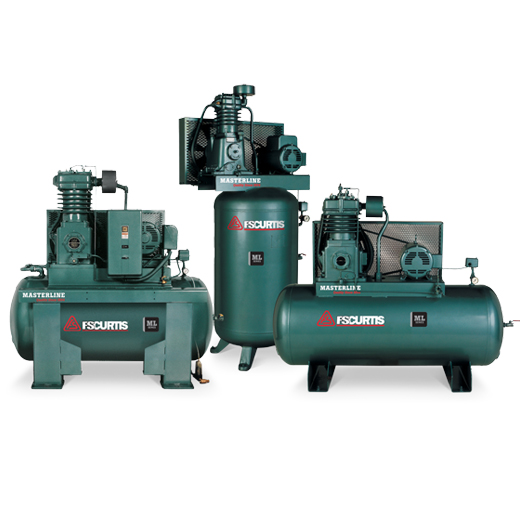
Interested in learning about industrial air compressor sustainability? Sustainability is a hot topic of conversation lately. In fact, the Compressed Air & Gas Institute notes three of the top benefits for compressed air: energy, environment, and cost. When most people think of industrial air compressors, sustainability is not what first comes to mind. However the […]
How To Best Care for an Industrial Air Compressor This Summer
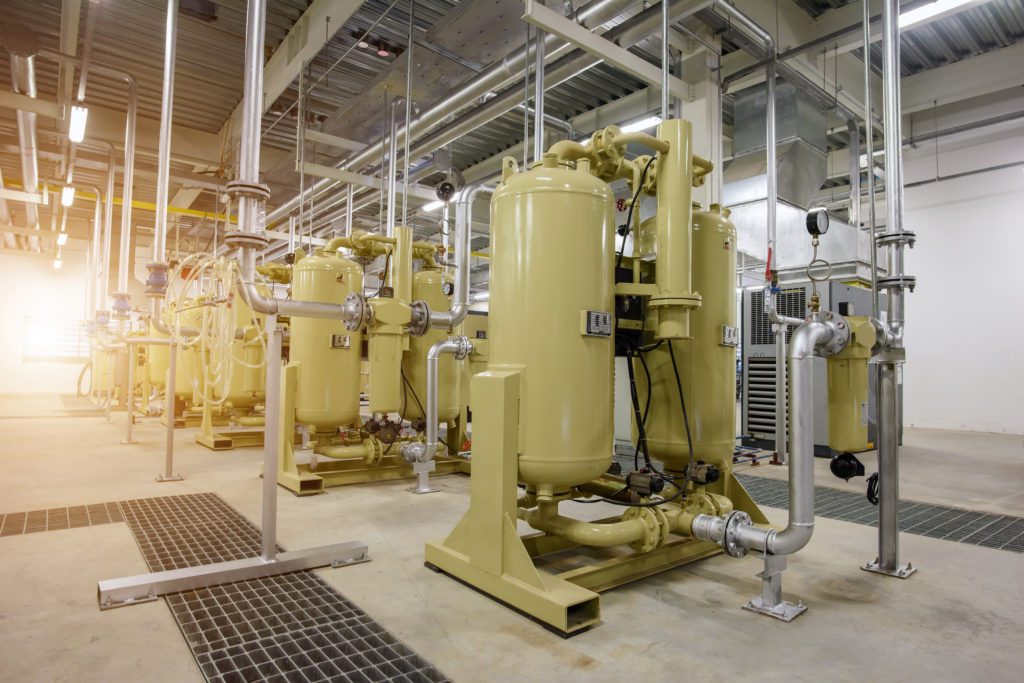
It may be a scorcher out there, but do not let your industrial air compressor unit suffer because of it this summer. Step 1: Choose The Right Industrial Air Compressor Choose the right air compressor and solidify your needs before selecting a unit: technology, size, ect. We suggest custom fabrication because curating your best option […]
Sizing an Industrial Air Compressor to Fit Your Needs
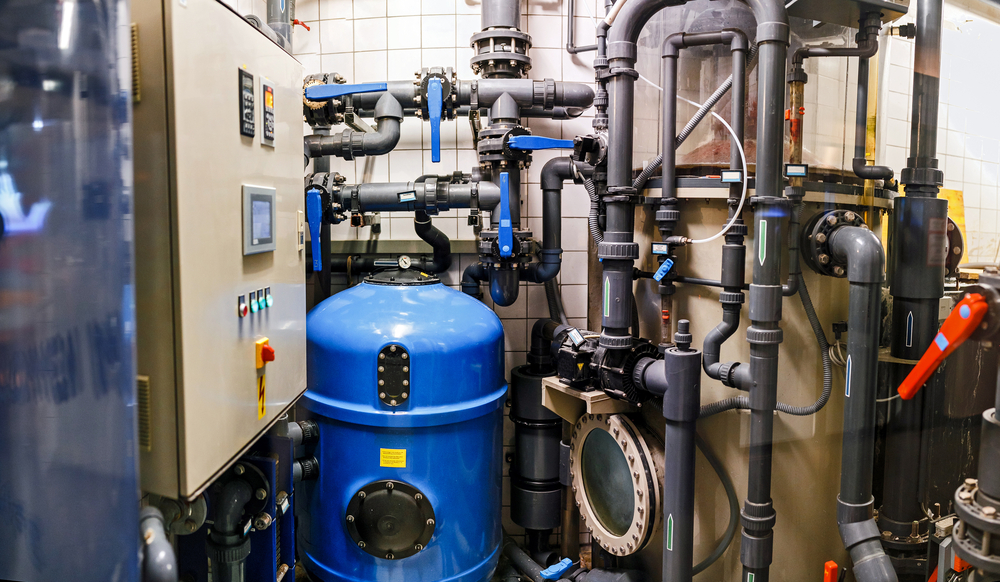
Sizing a new industrial air compressor can feel like a difficult task. It requires knowledge of the pressure and flow needed for the application. A solid understanding of how frequently jobs are performed and how many jobs are being completed at once. This may seem like a substantial amount of work, but the benefits of […]
Industries that Use Air Compressors Everyday
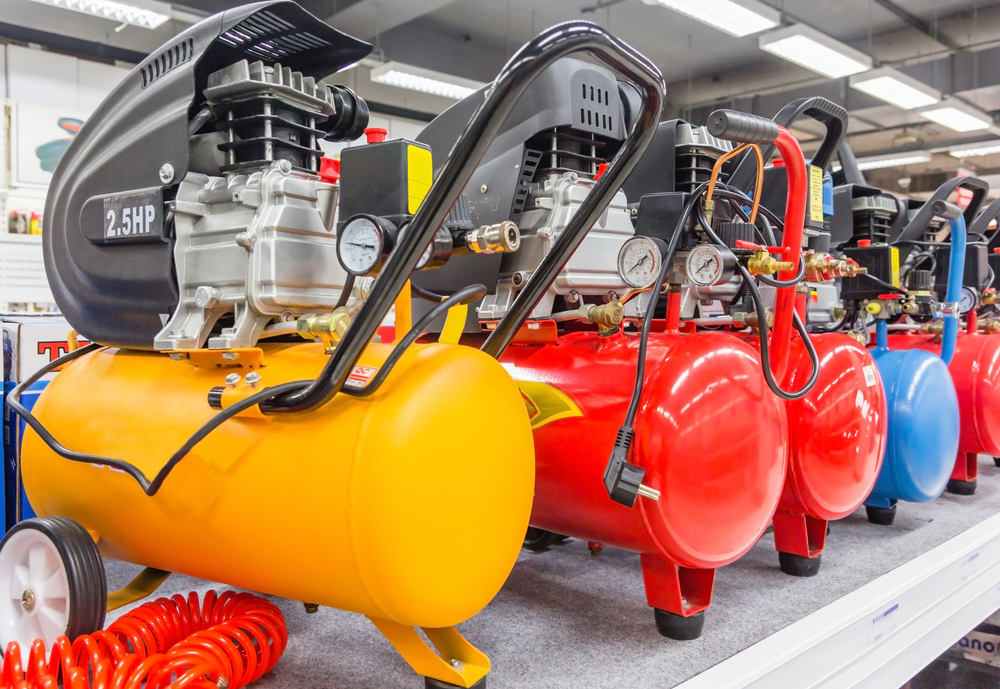
Dozens of industries have saved time and labor by using air compressors and have become reliant on them over the years. The applications of air compressors are nearly endless. For instance, the food you eat, the painkillers you take, the car you drive, and heck, even the chair you’re sitting on right now all have […]
Choosing the Right Air Compressor Oil: For Dummies
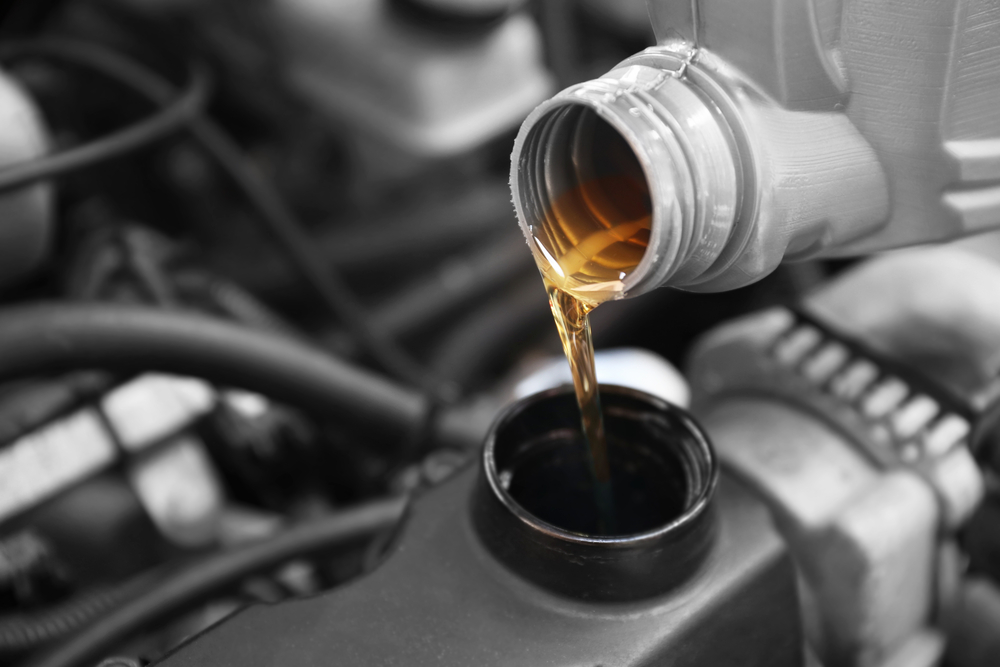
Just like different car models require a specific type and grade of oil for the best performance, the same is true for air compressors. When you use the right oil in your air compressor, it will benefit your machine in more ways than one. These benefits include a reduction in energy consumption, a decrease in […]
How to have a Healthy Relationship with Your Air Compressor
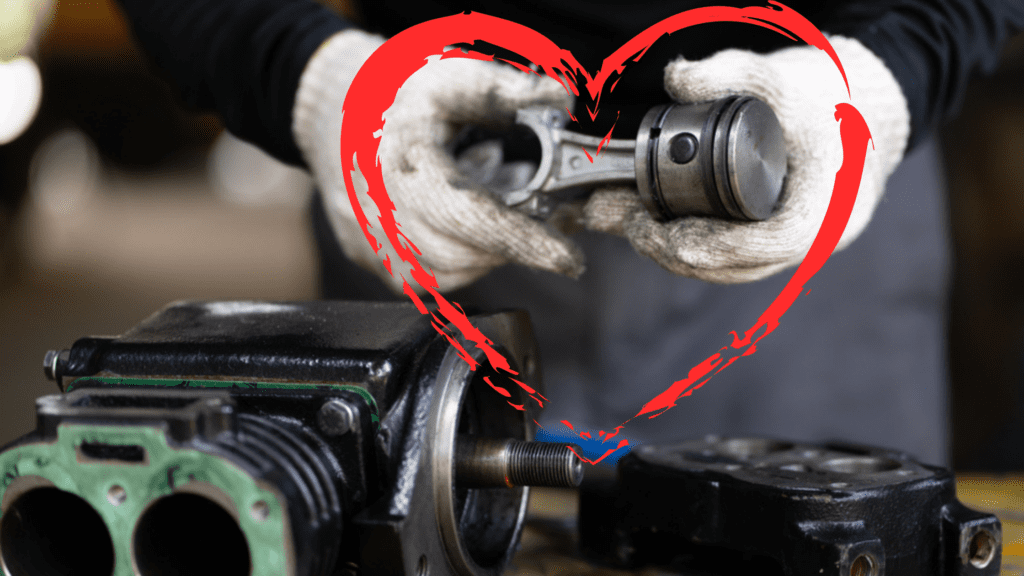
Unless you’ve been living in a cave your whole life, you know that today is Valentine’s Day. You may be celebrating with a significant other, treating yourself to a tub of ice cream, or hanging with some friends. But, have you ever thought about showing your air compressor system some love? With any healthy relationship, […]
Avoid Choosing the Wrong Industrial Compressor this Year!
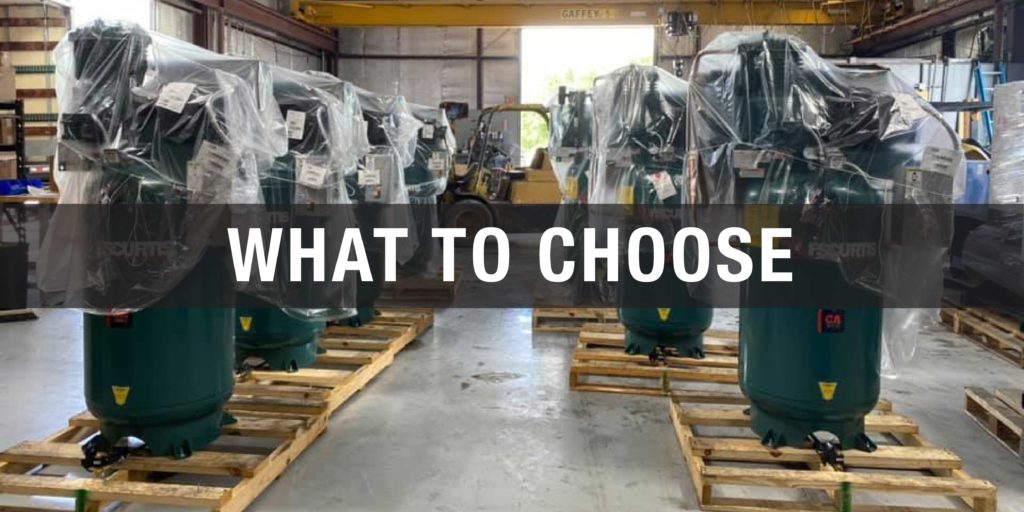
Choosing the right industrial compressor for your business can be tough. You have to sort through the compressors technologies, sizes, CFM (cubic feet per minute) and PSI (pounds per square inch) requirements, and other specs to determine which air compressor would best fit. Here are some common mistakes to avoid when choosing your industrial compressor: […]
Prepping your Air Compressor for Winter
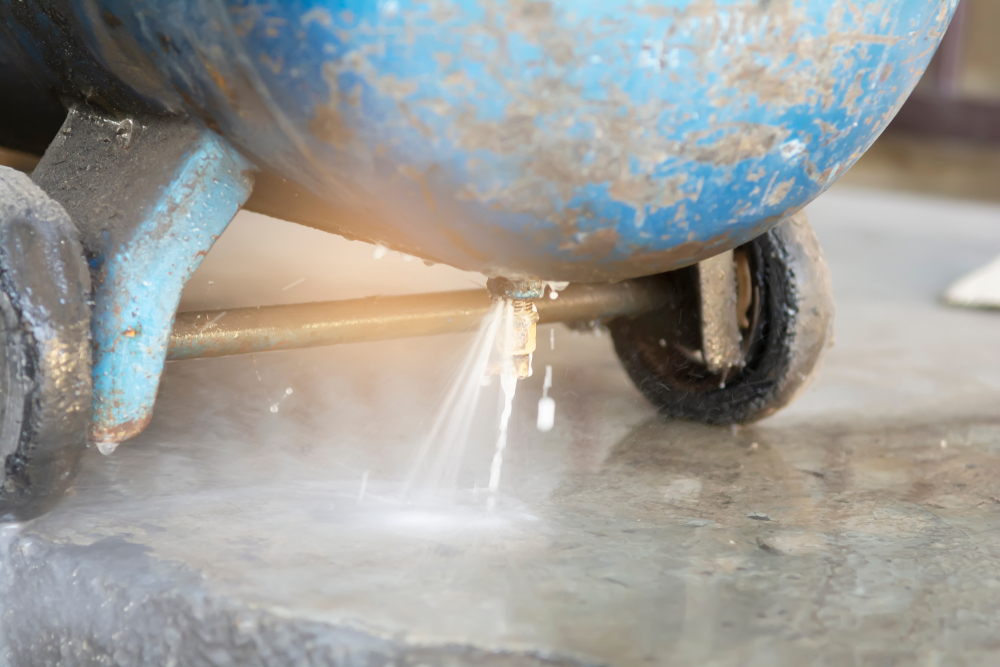
It’s getting to that time of the season where us Texans bring out our winter coats and slip on gloves before we head out to work. Just as we prepare ourselves for the winter months, our air compressors need some prep work to navigate properly through the cooler temperatures. Prepping your air compressor helps malfunctions […]
3C Loves Our Veterans
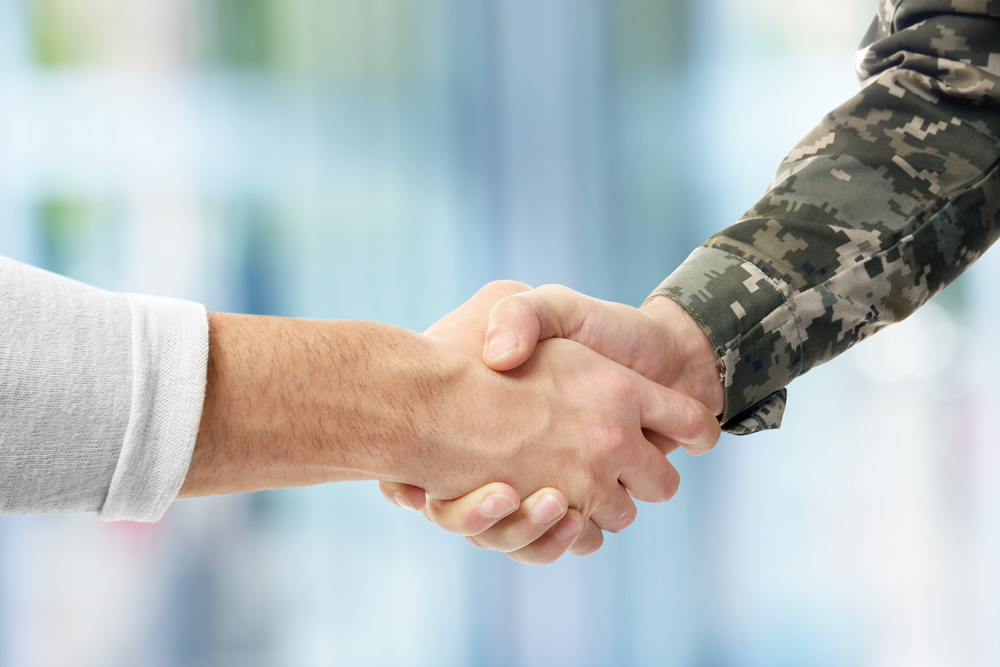
3C is proud to be a Veteran owned and operated company. We are honored to be a place of employment for other retired military men and women alike. In honor of Veterans Day, we are featuring a few of our Veterans on the 3C team. Meet Chase Stokley From 2013 – 2017, Chase served in […]