State of the Industry: Air Compressors 2021
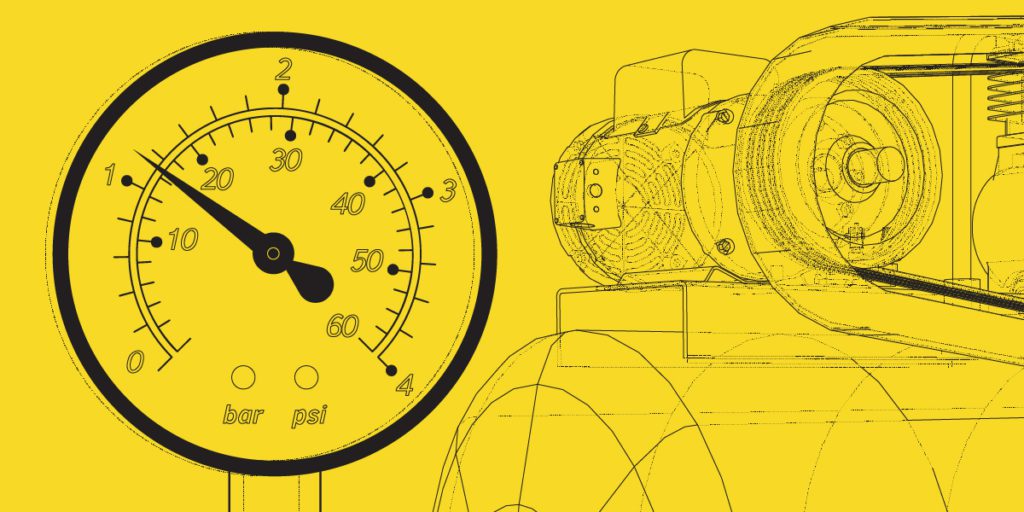
3C Industrial is in the business of air compressors. Anything and everything you need to know about air compressors, we have an answer. We want to take a quick look at the state of the industry for air compressors. We’re looking at what the market is doing now, where it’s going and how 3C fits […]
New or Used Air Compressor: Which One Is Best?
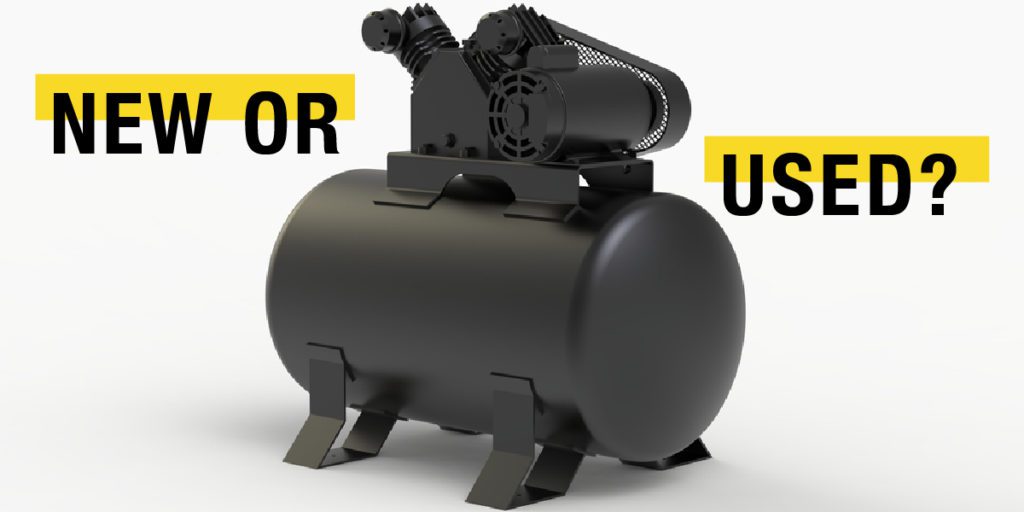
When looking for an air compressor, you can choose between buying new or used. This decision comes after deciding the specific type of compressor you need. There are plenty of pros and cons for either option and diverse factors to your choice. We’re here to help you outline the advantages and disadvantages of a new […]
Does Your Compressor Need an Upgrade?
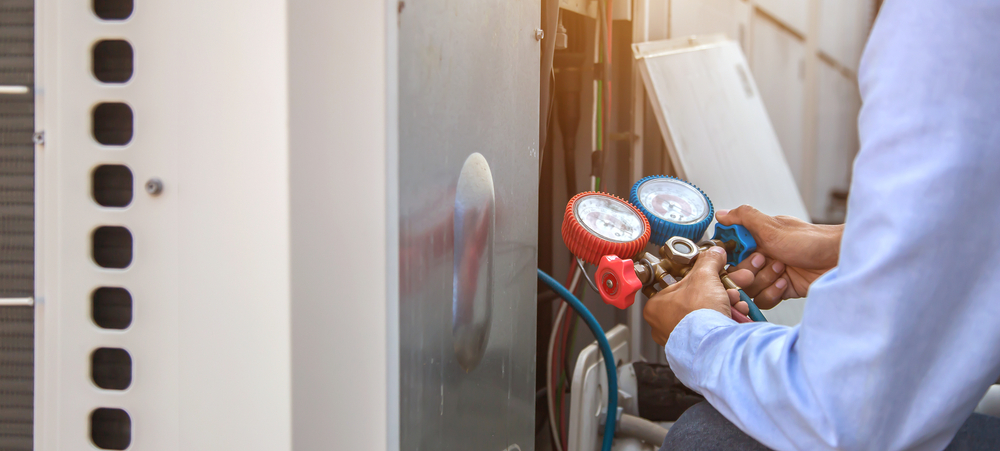
Are you doing corrective maintenance more and more every quarter? Are you shouting when chatting near your compressor? Do these scenarios sound familiar? These are all telltale signs that it may be time to upgrade your air compressor. Are you exceeding repairs? A good rule of thumb most of our customers follow on repairs is […]
Summer Maintenance Tips
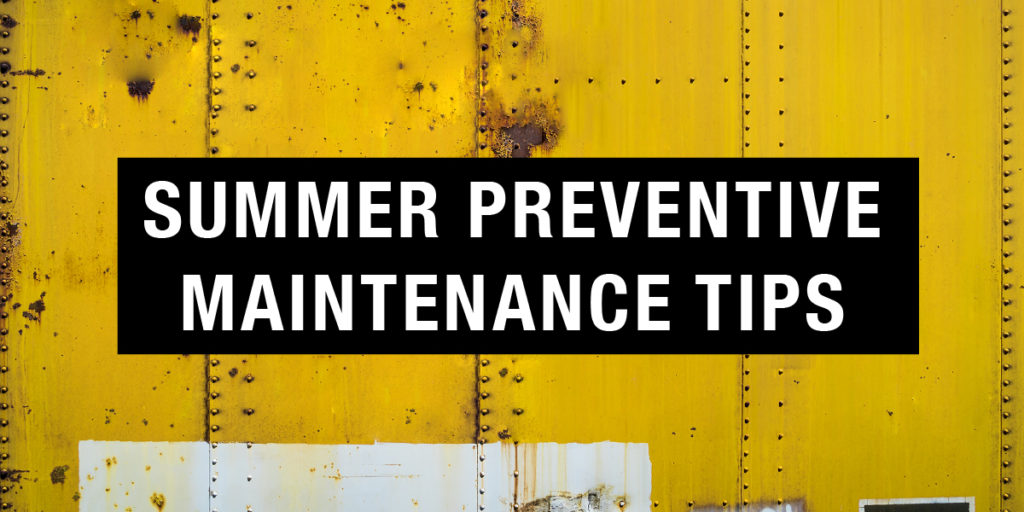
Summertime is officially here in Texas. The summer brings long, hot and humid days, all of which can take a toll on your air compressor. Skyrocketing temperatures combined with condensation can strain your equipment’s performance unless you’re prepared. Here are some summer maintenance tips that we at 3C have put together to help you with […]
Everything You Need to Know About Compressed Air Piping
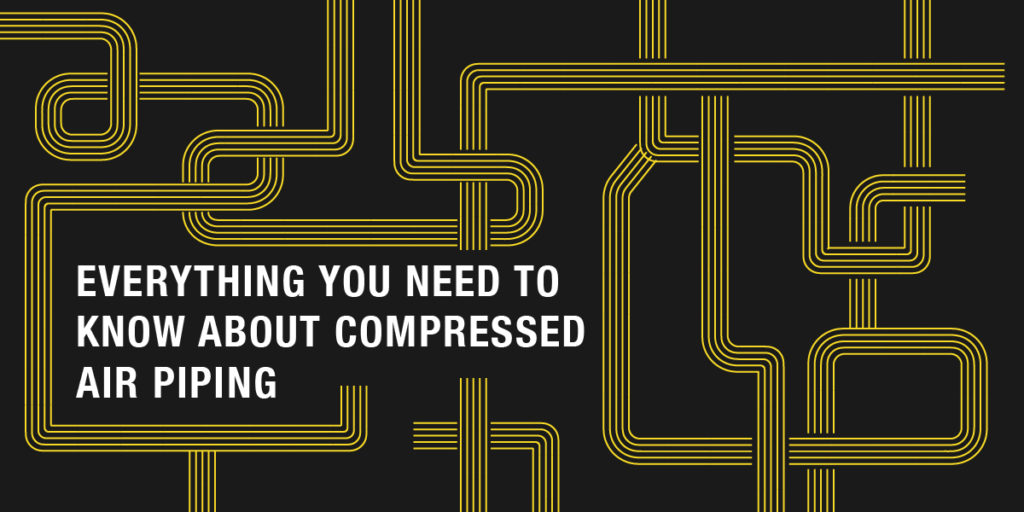
Traditional air piping is not always the most effective or efficient way to maintain your business. On top of that, you’ll also find your energy prices could be increasing. This where compressed air piping comes in. What is Compressed Air Piping? The purpose of an air piping system is to deliver compressed air to where […]
A Quick History of the Air Compressor
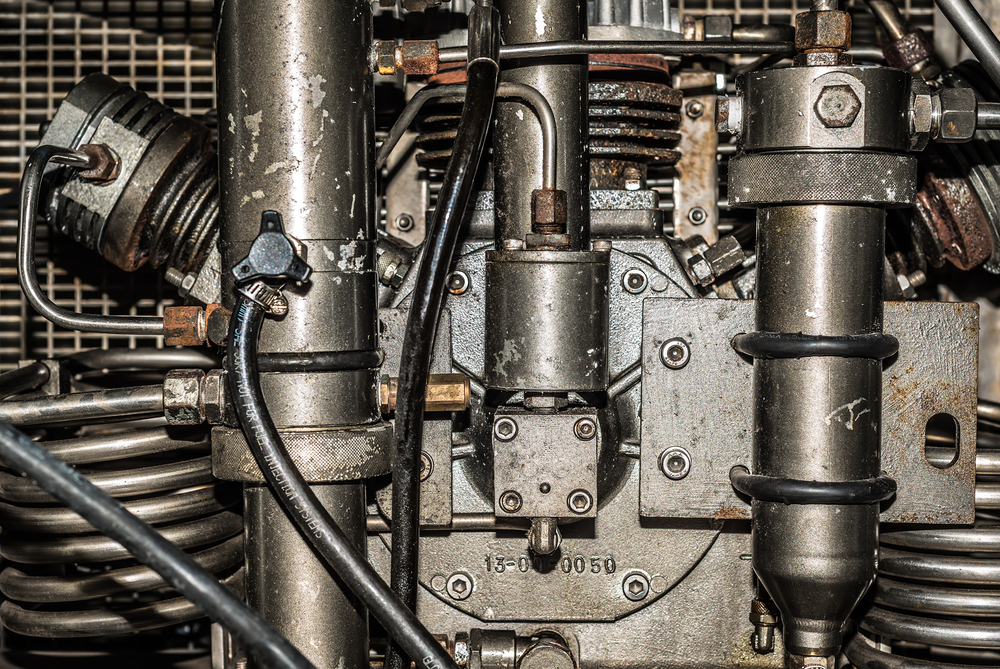
Air compressors are used in a variety of settings for multiple purposes. Today, compressors are used in agricultural, power engines, medical, mining, oil & gas and manufacturing industries. The air compressor helps in an array of ways, but back in the day they weren’t as versatile. They required a lot more manual activity than they […]
Air Compressor Preventive Maintenance – What All Does it Entail?
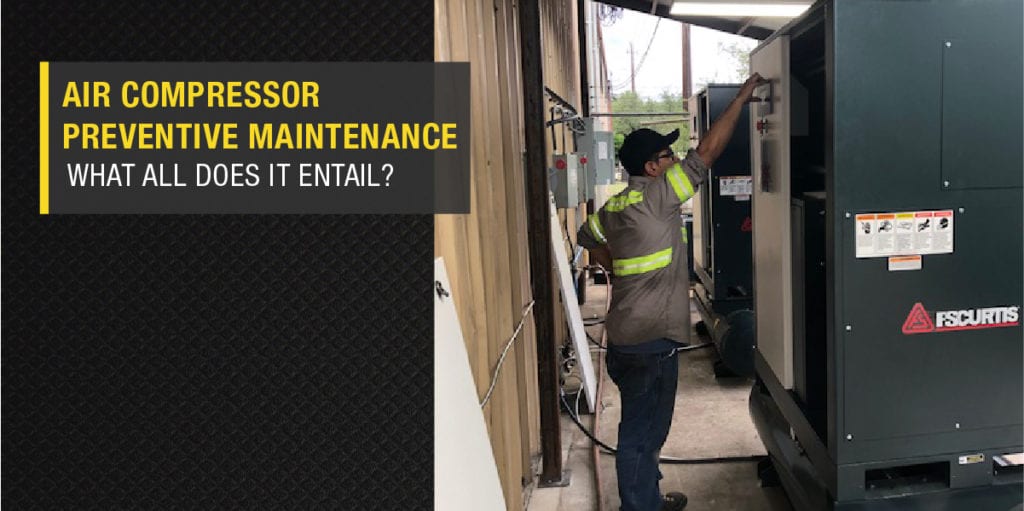
Preventive Maintenance is an essential part of keeping your air compressor running at optimal levels. Although PM can seem costly if you aren’t used to regularly servicing your compressor, the biggest expense you face is downtime should your equipment fail. What exactly is included in a PM service? There are two intervals at which you […]
Which Air Compressor Is Right For You?
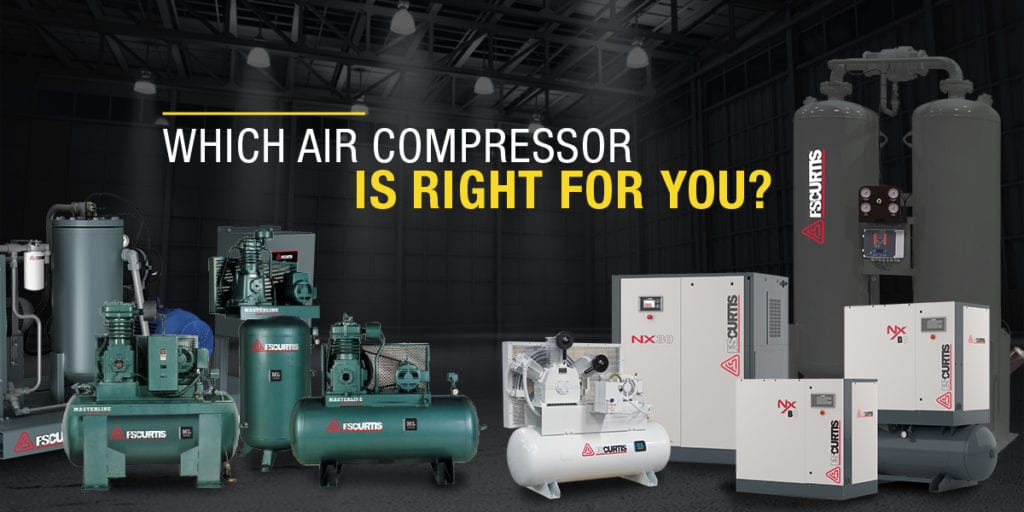
Choosing the Right Air Compressor Industries everywhere rely on air compressors to carry out a variety of functions, but not all compressors are the same. Here are some questions to ask yourself in order to determine which air compressor is right for you How much air do I need?Each tool or piece of equipment in […]
Air Treatment Mythbusting, Pt. 2
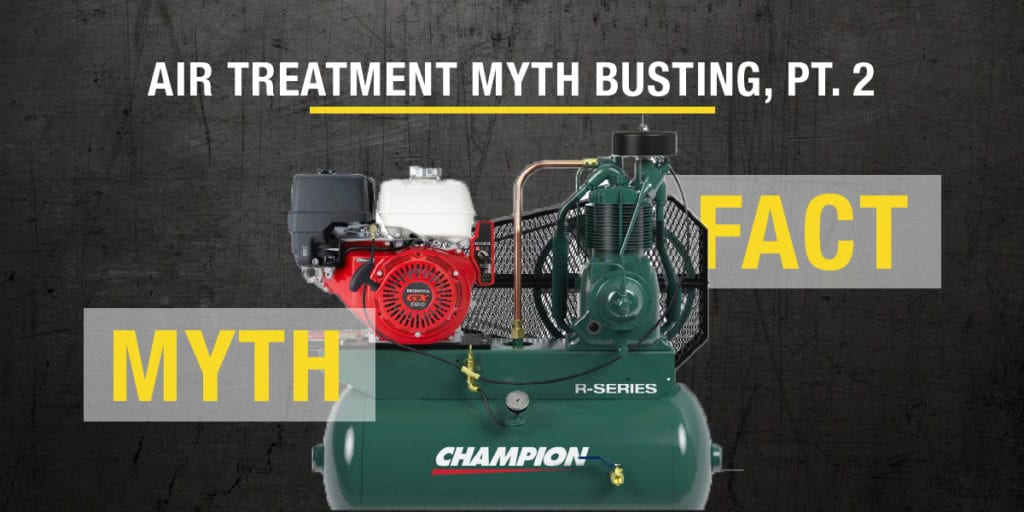
Myth: Compressed air contamination is a compressor issue. Fact: In a typical compressed air treatment system, contamination comes from three different sources, these being: Atmospheric air: Air compressors draw in huge amounts of atmospheric air, which continuously fills the system with contaminants such as water vapor, microorganisms, atmospheric dirt, and oil vapor. The air compressor: […]
What You Need to Know About Air Compressor Maintenance
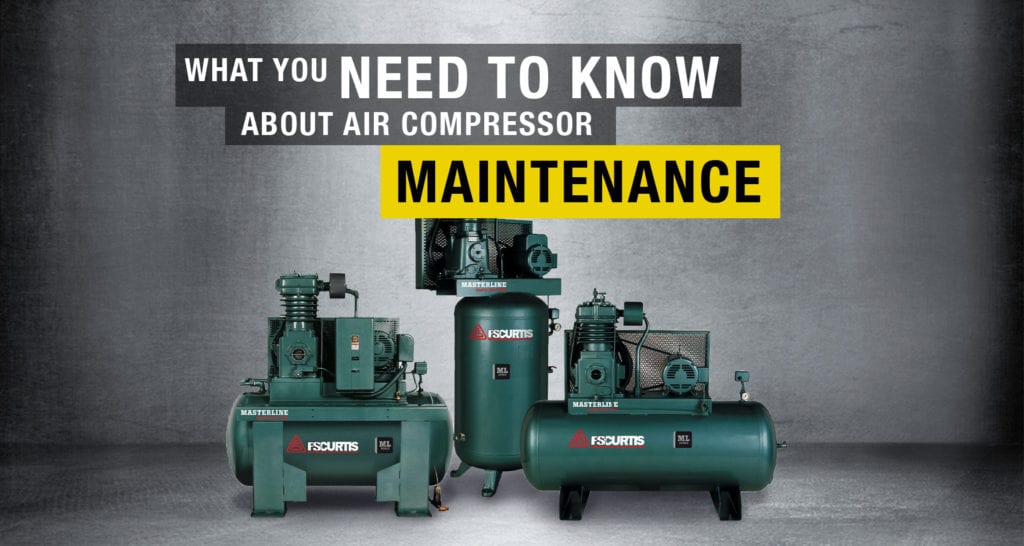
Regular maintenance of your air compressor is a great way to save yourself time and money. Taking a few moments out of your day to ensure things are running smoothly can keep your machine from developing major issues down the road that could cost a lot to repair. Be sure to hang on to your […]